Колінчастий вал КаМАЗ 740виготовляється з високовуглецевої сталі методом гарячого штампування а також зміцнюється за допомогою азотування або ж загартуванням струмами високої частоти (ТВЧ). Загартуванню піддаються шатунні і корінні шийки. має чотири шатунних шийки і п'ять корінних опор, які пов'язують щокі. Шатунниє шийки вала виготовлені так, що мають всередині порожнини, які закриваються заглушками. Порожнини розраховані на додаткове очищення масла за допомогою відцентрових сил.
Для врівноваження відцентрових сил на так званому шкарпетці (передньому кінці коленвала) і хвостовику (задньому кінці коленвала) встановлені противаги які на щоках вони виконані в цілому з валом, а на носик напресовують в момент складання і зафіксовані за допомогою сегментної шпонки.
На передньому кінці колінчастого вала закріплена шестерня приводу насоса масляного, вона є провідною, а на хвостовику (задньому кінці) - шестерня з маслоотражателем розподільна. У передній частині (носика) колінчастого вала виконані отвори використовуються для установки напівмуфти. У передній частині хвостовика - два отвори призначені для запресовування штифтів фіксують маховик, осьовий отвір для опорного підшипника первинного вала коробки передач і різьбові отвори для болтів кріплення маховика.
Можливість осьових зсувів виключається фіксацією вала за допомогою чотирьох наполегливих сталеалюмінієвих півкілець, які встановлюються в виточки блоку-картера двигуна і кришки корінної опори. На задній частині (на хвостовику), колінчастий вал ущільнений сальником запресованим в картер маховика.
Роль шатунних і корінних підшипників виконують вкладиш які встановлюються в так звані - ліжку. Вкладиші як корінні так і шатунні виготовляються із сталевої стрічки, яка покрита шаром свинцювата бронзи. У корінних вкладишах верхні і нижні частини не є взаємозамінними, так як на верхніх розташовані отвори підводять масло і канавки його розподіляють. А ось половинки шатунних вкладишів взаємозамінні.
В процесі роботи двигуна відбувається зношування шийок колінчастого вала КаМАЗ, і його дозволяється шліфувати чотири рази, а вкладиші існують випускаються в семи ремонтних розмірах.
Але ще однією особливістю клонували КаМАЗ є те, що блок і шатуни теж можна розточувати в розмір.
Ремонтні розміри шийок колінчастого вала і ліжок під вкладиші
шатунний підшипник | корінний підшипник |
||||
діаметр, мм | маркування вкладиша | діаметр, мм | маркування вкладиша верхнього (нижнього) |
||
шийки колінчастого вала | ліжку шатуна | шийки колінчастого вала | ліжку блоку |
||
740.1004058 Р1 79,50-85,0 | 740.1005170 (740.1005171) Р1 94,50-100,0 |
||||
740.1004058 Р2 79,00 | 740.1005170 (740.1005171) Р2 94,00-100,0 |
740.1004058 РЗ 80,00-85,00 | 740.1005170 (740.1005171) РЗ 95,00-100,5 |
||||
740.1004058 Р4 79,50-85,5 | 740.1005170 (740.1005171) Р4 94,50-100,5 |
||||
740.1004058 Р5 79,00-85,0 | 740.1005170 (740.1005171) Р5 94,00-100,5 |
||||
740.1004058 Р6 78,50-85,00 | 740.1005170 (740.1005171) Р6 93,50-100,0 |
||||
740.1004058 Р7 78,00-85,0 | 740.1005170 (740.1005171) Р7 93,00-100,0 |
клейма ремонтного розміруі діаметрів шийок колінчастого вала і ліжок в блоці або шатуне наносяться на тильну сторону вкладиша недалеко від площини роз'єму.
маховик(Рис.2) необхідний для накопичення кінетіческойенергіі протягом робочого ходу і обертання колінчастого вала під час допоміжних тактів, а також для виведення поршня з мертвих точок і зменшення нерівномірності обертання валу.
Маховик відлив з спеціального сірого чавуну. Він закріплений на задньому торці колінчастого вала вісьмома болтами 3 з легованої сталі. Точна фіксація маховика на колінчастим валу досягається за допомогою двох настановних штифтів, запресованих в торець колінчастого вала. На оброблену циліндричну поверхню маховика напрессован зубчастий вінець 1, призначений для з'єднання з шестернею валу стартера під час пуску двигуна. На задньому торці маховика встановлюється зчеплення. Для регулювання двигуна на маховику є паз під фіксатор 2 маховика і 12 отворів для провертання колінчастого вала ломиком.
ВСТУП
Витрати на забезпечення працездатності автомобілів за весь термін служби в кілька разів перевищують витрати на їх виготовлення. Значна частка витрат і простоїв в ремонті доводиться на двигун (до 30%), в тому числі на кривошипно-шатунний механізм (до 25%). На жаль однією з основних причин таких витрат є використання стратегії усунення відмов, що в середньому в 5-7 разів дорожче, ніж при попередженні відмов. Для зниження витрат на ремонт доцільна профілактична стратегія.
В процесі експлуатації автомобілів відбувається зміна їх технічного стану, Основними причинами якого є зношування, втомне руйнування, пластична деформація, корозія. Пластична деформація і утомлююча руйнування є наслідком конструктивно-технологічних недоробок або порушення правил експлуатації. Зазначені явища викликають, в тому числі, задираки шийок колінчастого вала через провертання вкладишів, а також розлом колінчастого вала, що є однією з основних причин ремонту двигунів Євро-2 КАМАЗ-740.
Надійна робота колінчастого вала залежить в основному від товщини масляної плівки в сполученні вкладиш-шийка вала, перепаду температур, наявності абразивних частинок, роботи елементів системи подачі масла. Причин провертання шатунних і корінних вкладишів присвячена велика кількість робіт, проте проблема задирака шийок, ремонтопридатності колінчастого вала, зниження експлуатаційних витрат, виявлення і усунення причин провертання вкладишів повністю не вирішена до теперішнього часу.
Простої автомобілів КАМАЗ викликані відмовами двигунів, характеризуються головним чином проворачиванием вкладишів і необхідності ремонту або заміни колінчастого вала. Експлуататорами автомобілів робляться певні заходи щодо виконання вимог заводу-виготовлювача, що стосуються організації технічного обслуговування, застосування моторних масел, захисту двигуна від попадання пилу і інших. У свою чергу конструктора ввели ряд поліпшень в конструкцію двигуна, спрямованих на підвищення ефективності очищення масла від абразивних частинок. Однак проведені заходи не виключили відмов двигунів КАМАЗ через вихід з ладу колінчастого вала.
Аналізу причин провертання вкладишів, як основного джерела несправності кривошипно-шатунного механізму присвячені багато робіт. У них стверджується зв'язок відмов підшипників колінчастого вала з ізноснимі характеристиками, визначальними величини граничних зносів шийок і вкладишів. Дослідженню шляхів зниження витрат на підтримку автомобіля в технічно справному стані в процесі експлуатації присвячені численні роботи таких вчених: М.А. Масин, Н.І. Іващенко, Ф.Н. Авдонькіна, М.А. Григор'єва, Н.Я. Говорущенко, Н.С. Ханіна, А.Г. Ліпкінда, В.А. Шадрічесва, А.І. Ліпгарта, Е.С. Кузнєцова, І.Є. Дюміна, Г.В. Крамаренко.
Позначимо мета і об'єкт дослідження:
Мета дослідження: розробка способу ремонту колінчастого вала з випливають зниженням витрат на ремонт двигуна.
Об'єкт дослідження: азотований колінчастий вал двигунів КАМАЗ Євро-2, кривошипно-шатунний механізм, система мастила.
Предмет дослідження: неможливість використання колінчастого вала двигунів Євро-2 КАМАЗ після шліфування шийок на глибину понад 0,25 мм.
Наукова новизна полягає в розробці оригінальної методики ремонту, що дозволяє відновлювати азотований колінчастий вал двигунів КАМАЗ Євро-2.
Практична цінність: розроблена методика відновлення азотованих колінчастих валів двигунів КАМАЗ Євро-2. Має цінність для заводу-виготовлювача, фірмових сервісних центрів і ремонтних заводів. Це дозволить:
а). підвищити надійність двигунів в експлуатації;
б). значно зменшити вартість ремонту автомобілів.
РОЗДІЛ 1. Аналіз стану питання по ремонту азотованих колінчастих валів автомобілів КАМАЗ
1 Азотований колінчастий вал КАМАЗ
Азотований колінчастий вал двигуна Євро-2 КАМАЗ-740 (рис. 1.1.1.) Виготовлений з високоякісної сталі і має п'ять корінних і чотири шатунні шийки, пов'язані щоками і пов'язані перехідними галтелями. Для рівномірного чергування робочих ходів шатунні шийки колінчастого вала розташовані під кутом 90 °.
Зміцнення колінчастого вала виробляється азотуванням на глибину 0,5 ... 0,7 мм, твердість зміцненого шару не менше 600 HV.
Підведення масла до шатунних шийок проводиться через отвори в корінних шийках 6 і отвори 5.
Малюнок 1.1.1. Азотований колінчастий вал КАМАЗ
противагу; 2 - шестерня приводу масляного насоса; 3 - заглушка; 4 шпонка; 5 - отвори підведення масла до шатунних шийок; 6 - отвори підведення масла в корінних шийках.
Для врівноваження сил інерції і зменшення вібрацій колінчастий вал має шість противаг, відштампованих заодно зі щоками колінчастого вала. Крім основних противаг, є додатковий знімний противагу 1, напресованими на вал, його кутове розташування щодо колінчастого вала визначається шпонкою 4.
На хвостовику колінчастого вала виконана шийка, по якій центрируется шестерня колінчастого вала і маховик. На задньому торці колінчастого вала виконано десять різьбових отворів М16х1,5-6Н для кріплення шестерні колінчастого вала і маховика, на передньому торці виконано вісім різьбових отворів M12x1,25-6Н для кріплення гасителя крутильних коливань.
Номінальні діаметри шийок колінчастого вала:
- корінних 95-0,015 мм;
- шатунних 80-0,013 мм.
Для відновлення двигуна передбачені вісім ремонтних розмірів вкладишів (табл. 1.1.1., 1.1.2.).
Таблиця 1.1.1 Таблиця ремонтних вкладишів корінних підшипників колінчастого вала
ОбозначеніеДіаметр корінний шийки, ммДіаметр отвори в блоці циліндрів, мм7405.1005170 Р0 7405.1005171 Р094,951007405.1005170 Р1 7405.1005171 Р194,51007405.1005170 Р2 7405.1005171 Р2941007405.1005170 Р3 7405.1005171 Р395100,57405.1005170 Р4 7405.1005171 Р494,5100,57405.1005170 Р5 7405.1005171 Р594100,57405.1005170 Р6 7405.1005171 Р693,51007405.1005170 Р7 7405.1005171 Р793100
Таблиця 1.1.2. Таблиця ремонтних вкладишів нижньої головки шатуна
ОбозначеніеДіаметр шатунной шийки, ммДіаметр отвори в кривошипної головцішатуна, мм7405.1004058 Р079,95857405.1004058 Р179,5857405.1004058 Р279857405.1004058 Р38085,57405.1004058 Р479,585,57405.1004058 Р57985,57405.1004058 Р678,5857405.1004058 Р77885
Межі допусків діаметрів шийок ремонтного колінчастого вала при відновленні двигуна повинні бути такими ж, як у діаметрів шийок нового колінчатого вала.
Клеймо ремонтного розміру нанесено на тильній стороні вкладиша.
Вкладиші 7405.1005170 Р0, 7405.1005171 Р0, 7405.1005058 Р0 застосовуються при відновленні двигуна без шліфування колінчастого вала. При необхідності шийки колінчастого вала поліруються.
Межі допусків за діаметрами шийок колінчастого вала, діаметру отвору в блоці циліндрів і діаметру отвору в кривошипної головцішатуна при відновленні двигуна повинні бути такими ж, як у номінальних розмірів.
Маркування колінчастого вала, виконана в поковки на третьому противазі, повинна бути 740.50-1005020.
Важливо! При шліфуванні колінчастих валів, зміцнених азотуванням або карбонітруванні, на глибину по корінним шийок до 94 мм і менше або по шатунним шийок до 79 мм і менше, необхідне проведення повторної зміцнюючої обробки за спеціальною технологією.
1.2 Колінчастий вал КАМАЗ, зміцнений струмами високої частоти
На двигунах рівня Євро-3 застосовується той же колінчастий вал з маркуванням 740.50-1005020, проте з 2008 року для двигунів потужністю до 320 к.с. включно допускається застосування колінчастих валів зміцнених струмами високої частоти з відповідним маркуванням 740.50-1005020-10.
Так само в зв'язку з високими питомими навантаженнями, що діють на підшипники в двигунах нового покоління, вкладиші двигунів Євро-3 мають конструктивні відмінності від раніше випущених (табл. 1.2.1., 1.2.2.), Спрямовані на підвищення їх працездатності, при цьому змінена маркування вкладишів на 740.60-1004058 (шатунні), 740.60-1005170 і 740.60-1005171 (корінні).
При ремонті колінчастого вала допускається перешліфовка корінних і шатунних шийок зі зменшенням їх діаметрів на 0,25 мм і застосуванням відповідних ремонтних типорозмірів корінних і шатунних вкладишів.
Таблиця 1.2.1 Таблиця ремонтних вкладишів корінних підшипників колінчастого вала
ОбозначеніеДіаметр корінний шийки, ммДіаметр отвори в блоці циліндрів, мм740.60-1005170 Р01 740.60-1005171 Р0194,75100740.60-1005170 Р02 740.60-1005171 Р0295,5100740.60-1005170 Р03 740.60-1005171 Р0394,25100740.60-1005170 Р10 740.60-1005171 Р1095100,5740.60- 1005170 Р11 740.60-1005171 Р1194,75100,5740.60-1005170 Р12 740.60-1005171 Р1295,5100,5740.60-1005170 Р13 740.60-1005171 Р1394,25100,5
Таблиця 1.2.2. Таблиця ремонтних вкладишів нижньої головки шатуна
ОбозначеніеДіаметр шатунной шийки, ммДіаметр отвори в кривошипної головцішатуна, мм740.60-1004058 Р0179,7585740.60-1004058 Р0279,585740.60-1004058 Р0379,2585740.60-1004058 Р108085,5740.60-1004058 Р1179,7585,5740.60-1004058 Р1279,585,5740.60-1004058 Р1378,2585,5
1.3 Властивості азотованих колінчастих валів
Азотування має ряд переваг і недоліків.
Головним достоїнством технології азотування є висока твердість зміцненого шару, HV до 1200.
Азотований колінчаті вали КАМАЗ, виготовлені зі сталі марки 42ХМФА ТУ 14-1-1296-75 мають твердість в районі 800 HV, при вимогах креслення не менше 600 HV. наступним позитивним моментомазотированного колінчастого вала може бути те, що при азотуванні відбувається поверхневе насичення всієї деталі, а не тільки шийок як при індукційному гартуванню. Це підвищує міцність вала на вигин.
До недоліків можна віднести цілий ряд факторів:
Процес азотації займає досить тривалий час, до 30 годин і більш трудомісткий щодо виконання;
Товщина зміцненого шару складає не більше 0,5-0,7 мм;
Зміцнений шар з високою твердістю важко обробляємо;
Насичення нитридами всій поверхні вала в той же час знижує його пластичність;
При перегрів азотированного ділянки відбувається його розрив, а не розширення як у випадку з ТВЧ.
1.4 Аналіз дефектів колінчастих валів КАМАЗ
Причини виходу з ладу
Статистика за видами зносів і дефектів колінчастих валів, котрі вступили з двигунами КАМАЗ в капітальний ремонтна ЗАТ «Ремдизель» м Набережні Челни, показує (табл. 1.4.1.) структуру дефектів, їх повторюваності і поєднаннях.
Таблиця 1.4.1. Розподіл основних дефектів колінчастих валів
Найменування дефектовДоля% задирака на шатунних шийках через провороту вкладишів (В) Тріщини на шиях Прогин осі коленвала більш 0,9мм (виміряно за третій корінний шийки) задирака на корінних шийках через провороту вкладишів (Г) Ні галтелів на шиях (неякісна перешліфовка) Втомне руйнування коленвала34,92 9,41 5,05 4,54 5,76 0,70
Перші чотири дефекту, зазначені в таблиці, як правило, зустрічаються одночасно. Колінчасті вали з задираками по шийок мають тріщини і прогин осі. Місця розташування дефектів показані на рис. 1.4.1., Позначені буквами: А, Б - заломи і задираки болтів на передньому і задньому торцях, В - знос шатунних шийок, Г - знос і задираки корінних шийок, Е - задираки поверхні під підшипник первинного валу, І - знос наполегливих поверхонь півкілець, Д - поверхні під сальник, смятие пазів шпон, Ж - забоіни на противовесах.
Мал. 1.4.1 Місця розташування дефектів колінчастого вала
За даними ВНІІТУВІД «РЕМДЕТАЛЬ» (ГОСНИТИ) в результаті аналізу експлуатаційних дефектів колінчастих вала двигуна КАМАЗ було встановлено, що з 11 найменувань дефектів найбільш поширеними дефектами були наступні:
деформація колінчастого вала (69%);
проворот, задираки або аварійний знос корінних і (або) шатунних шийок (22%);
тріщини на корінних і (або) шатунних шийок (7%);
ослаблення посадки, смятие штифтів, дозвіл різьблення під болти кріплення маховика (19%).
Середня величина відхилення від номінального діаметра в зоні найбільшого зносу (при нормальному зносі) корінних шийок становить 0,027 мм, а шатунних 0,029 м.
Биття середньої шийки для нормально зношених валів знаходиться в межах від 0,02 мм до 0,17 мм, при цьому середня величина биття становить 0,054 мм, а для аварійного зносу в межах від 0,040 мм до 0,730 мм, при середній величині биття - 0,227 мм .
Причинами задирака шийок можуть бути кілька чинників. Це може 6ить масляне голодування при роботі корінних і шатунних підшипників колінчастого вала, а також перевищення похибки форми шийок більше 0,05 мм. Основне значення має несуча здатністьшийок, що залежить від триботехнические пари.
Аналіз результатів стендових випробувань опору втоми показав, що ці колінчаті вали мають значний запас міцності. У той же час їх показники істотно залежали від постачальників стали. Найбільш високі значення моментів витривалості мали колінчаті вали зі сталі Челябінського металургійного комбінату. При випробуваннях нормально зношених валів з шийками ремонтних розмірів значущого зниження опору втоми не було виявлено, що можна пояснити загартуванням галтелів.
Аналіз несправностей колінчастих валів двигунів КАМАЗ 740 Євро-2 за даними ІП Мухаметшин М.Х (місце проходження ПДП).
Основні причин виходу колінчастого вала з ладу:
проворот вкладишів;
зірвати заводський брак;
порушення норм і порядку технічного обслуговування;
заміна вкладишів «на вазі» без перешлифовки вала або розточування блоку циліндрів.
Для колінчастого вала 740.50-1005020 визначені наступні допустимі розміри:
Діаметр корінних шийок 94,985 ... 95,000
Зазор в підшипниках корінних шийок 0,096 ... 0,156
Допустимий зазор в підшипниках корінних шийок 0,22
Діаметр шатунних шийок 79,987 ... 80,000
Зазор в підшипниках шатунних шийок 0,16
Допустимий зазор в підшипниках шатунних шийок 0,070 ... 0.117
Осьової зазор 0,100 ... 0,195
Допустимий осьовий зазор 0,25
Діаметр шийки вала під передній противагу, шестерню приводу масляного насоса:
Номінальний 115,080 ... 115,110
допустимий 115,080
Діаметр шийки вала під задню шестерню колінчастого вала:
Номінальний 105,070 ... 105,096
допустимий 105,060
1.5 Дослідження ремонтопридатності колінчастих валів двигунів КАМАЗ
Дослідження проводилося в НТЦ ВАТ «КАМАЗ». Об'єкти дослідження:
колінчастий вал з зміцненим іонним азотуванням в ВАТ «КАМАЗ». Заміри мікротвердості виконані в НТЦ, протокол досліджень від 25.06.2003 р № 124;
колінчастий вал з зміцненням індукційної загартуванням. Заміри мікротвердості виконані в НТЦ, протокол досліджень від 07.07.2004 р № 465.
Дослідження ремонтопридатності колінчастих валів проводилося за допомогою виміру мікротвердості по HV0,3 по перетинах, перпендикулярних до досліджуваних поверхнях.
В якості технологічного параметра була обрана мікротвердість 453 HV. За результатами замірів будувався графік розподілу мікротвердості по глибині зміцненого шару для кожного колінчастого вала. Величина 453 HV - мінімальна твердість, яка допускається на шатунних і корінних шийках колінчастих валів з зміцненням індукційної загартуванням після ремонту двигунів КАМАЗ. Підтвердженням правильності вибору такої мікротвердості є випробування на надійність в обсязі 1000 годин роботи двигуна КАМАЗ-740.11-240, випробування № 311439 ВАТ «НІІТавтопром». Після закінчень випробування двигуна колінчастий вал знаходиться в працездатному стані, твердість поверхні шийок становить 454 ... 524 HV.
Результати дослідження показані на графіку 1.5.1.
Графік 1.5.1 Розподілу мікротвердості по глибині зміцнених шарів для різних способів зміцнення колінчастих валів
Аналіз ремонтопридатності колінчастих валів наведено в таблиці 1.5.1.
Таблиця 1.5.1 Аналіз ремонтопридатності колінчастих валів
СпособупроченіяСостояніе поверхні шийок перед ремонтомКатегорія ремонтопрігодності0,5 ...... 0,4коренние шейкішатунние шейкікоренние шейкішатунние шейкіПріпуск при перешліфовуванні, ммМікротвердость після шліфовкіРаботоспособностьПріпуск при перешліфовуванні, ммМікротвердость після шліфовкіРаботоспособностьПріпуск при перешліфовуванні, ммМікротвердость після шліфовкіРаботоспособностьПріпуск при перешліфовуванні, ммМікротвердость після шліфовкіРаботоспособностьІонное азотірованіеІзнос0,160455 + 180430-1,035n / a-1,055n / a-Задір0,193415-180430-1,068n / a-1,055n / a-Индукционная закалкаІзнос0,248576 + 180584 + 1,115517 + 1,055494 + Задір50% колінчастих валів не можуть бути відновлені через задирів і перегинів
З наведеного аналізу слід: колінчаті вали з природним зносом мають по шийок знос до 0,1 мм, тому значна кількість колінчастих валів може бути відновлено з використанням додаткових категорій ремонтних розмірів по шийок зі ступенями ремонту 0,25 мм по діаметру, що відповідаємо світовій практиці двигунобудування. Введення цих додаткових категорій ремонтних розмірів особливо актуально для колінчастих валів, зміцнених іонним азотуванням або карбонітруванні. Зважаючи на значне зниження зносів і глибини зміцненого шару в порівнянні з зміцненням індукційної загартуванням (рис. 1.4.1., 1.4.2.).
1.6 Конструктивно-технологічні заходи щодо підвищення ремонтопридатності колінчастого вала
ВАТ «КАМАЗ» впровадив наступні заходи для підвищення ремонтопридатності колінчастих валів власного виробництва.
№МеропріятіяЕффект1. 2. 3. 4. 5. 6. 7. 8. 9. 10. 11. 12.Задросселіровани другорядні споживачі масла за рахунок зменшення діаметрів маслоподводящие отворів опор розподільного вала з 8 до 4 мм Збільшено діаметр отвору в верхньому корінному вкладиші з 5 до 7 мм і збільшена ширина канавки у вкладиші з 5 до 7 мм Установка масляного насоса підвищеної продуктивності з 85 до 150 л / хв з удосконаленими клапанами Удосконалення очищення і охолодження масла фільтрами і теплообмінником Удосконалення колінчастого вала (відмова від відцентрових грязеуловителей і зміна масляних каналів) Установка маслооткачівающего насоса на деяких моделях двигунів Введено односторонній підведення масла до шатунних підшипників Ліквідовано втулка відцентрової очистки масла в шатунной порожнини Зменшення натягу шатунних вкладишів за рахунок зниження величини виступання і розміру у вільному стані Введення полірування масляних клапанів колінчастого вала Введена термообробка шийок ТВЧ замість азотування Впроваджено ін і ремонті перед перешліфовці правка осі коленвала карбуванням галтелейСокращена нерівномірність тиску масла з корінних опор на 20%. Витрата масла через шатунні підшипники підвищується на 35-40%, критичні режими спостерігаються при більш високих частотах. Підвищення тиску в системі мастила в середньому на 10%, створення запасу продуктивності. Підвищено ступінь очищення масла і покращився тепловий режим двигуна. Підвищення втомної міцності колінчастого вала, поліпшення мастила шатунних підшипників. Стабілізація роботи системи змащення в екстремальних умовах (тривалі крен). Підвищений тиск масла в корінних підшипниках на 0,06 - 0,17 МПа, знижено критичний тиск розриву потоку Знизилася тиск першого критичного режиму змащення шатунних підшипників. Зниження напруги у вкладишах і їх деформацій при роботі. Підвищення межі витривалості на 14-28%. З'явилася можливість перешліфовок в 4 ремонтних розміру з інтервлом 0,5 мм Знизився відсоток перескоків через ремонтний розмір і вибракування при перешліфовуванні
1.7 Завдання розробки способу ремонту азотированного колінчастого вала двигуна Євро-2 КАМАЗ-740
З пункту 1.3. випливають дві основні проблеми ремонтопридатності азотированного колінчастого вала КАМАЗ. Це питання видалення високоміцного азотированного шару і зміцнення азотированного колінчастого вала після шліфовки шийок на глибину більше 0,5 мм, тобто можливість застосування другого і наступних ремонтних розмірів.
1.7.1 Ремонт колінчастого вала. Видалення зміцненого шару
Як показує практика азотований колінчастий вал, що володіє високою міцністю, внаслідок чого традиційний метод ремонту колінчастого вала слабо застосуємо. Підвищена твердість металу негативно позначається на ресурсі абразивного круга шліфувального верстата. Ресурс кола зменшується в рази в місці з тим сам коло втрачає форму, зважаючи нерівномірного сточування. Між тим загальним правиломпри виборі кола по твердості є наступне: чим твердіше шліфований матеріал, тим швидше притупляються зерна кола, отже, тим м'якше повинен бути обраний коло (слабкіше зв'язка). Це передбачає застосування іншого шліфувального круга для обробки азотированного колінчастого вала, більш м'якого і разом з тим швидко розходяться.
Рішенням цієї проблеми може стати технологія шліфування шийок колінчастого вала електрохімічним методом на електроерозійному верстаті або технологією електроерозії.
1.7.2 Зміцнення колінчастого вала після шліфовки шийок на глибину більше 0,5 мм
Рішенням проблеми відсутності зміцненого шару може є подальша термічна обробка - індукційна гарт струмами високої частоти в заводських умовах. Процес загартування ТВЧ по тривалості займає 7-10 хвилин на вал, що в порівнянні з 30-годинним процесом азотування в помітному виграші.
Також, наприклад, може бути перейнятий метод, впроваджений в ТОВ «Науково-технічний, освітній та виробничий центр високочастотних електротехнологій« ИНТЕРМ ».
В якості приводу обертання може бути використаний шліфувальний верстат колінчастих валів.
Висновки по розділу
Колінчасті вали зміцнені іонним азотуванням можуть бути відновлені на категорію ремонтного розміру 0,5 при природному зносі в експлуатації.
2. Азотування колінчастих валів КАМАЗ маючи гідність як збільшення твердості зміцненого шару приховує в собі два суттєвих недоліки. Перше, це труднощі видалення зміцненого шару після проворота вкладишів чи іншого дефекту, що спричинило не вибір подальшого застосування колінчастого вала. Другий випадок, це відсутність зміцненого шару при ремонті колінчастого вала до другого ремонтного розміру. Для вирішення цих завдань розглядається застосування методів електрохімічної і термічної обробки колінчастого вала. Цим, а також іншим методам відновлення колінчастих валів присвячений другий розділ дипломного проекту.
РОЗДІЛ 2. Аналітичне дослідження технологій і способів ремонту колінчастих валів двигунів КАМАЗ
Перед виконанням ремонту колінчастого вала необхідно переконатися в його ремонтопридатності. Для цього необхідно виконати його дефектацию.
До дефектовке відноситься візуальний огляд, вимір геометричних розмірів, перевірка на биття і на відсутність мікротріщин. Необхідно визначити, чи залишиться після наступної операції шліфування достатній залишковий загартований шар у колінчастого вала.
При необхідності точну глибину загартованого шару колінчастого вала слід визначити на дефектному зразку такого ж колінчастого вала. Для цього його необхідно поступово сошлифовать, періодично перевіряючи його твердість за приладами Роквелла або Брюнель.
Можливі дефекти колінчастого вала, що підлягають відновленню:
знос / проворот шатунних і / або корінних шийок;
знос шийки носка;
знос шийки хвостовика;
тріщина на хвостовику;
деформація торця.
2.1 Шліфування колінчатих валів
Відновлення колінчастого вала по износам, задирам або проворот на поверхні шийок, деформації, скручування шийок проводиться перешліфовці в ремонтні розміри з наступним поліруванням і обробкою галтелів маслоподводящие отворі. До ремонтних розмірів, зазначених в таблицях 1.1.1., 1.1.2., 1.2.1. і 1.2.2. твердість поверхонь шийок зберігається без повторної термообробки.
Вали, що мають вигини більш допустимих, правляться з карбуванням по жолобник. Карбування по Жолобники проводиться для фіксації правки, величину биття перевіряють індикаторної стійкою. Пристосування для редагування виготовляється з використанням ручного гідравлічного домкрата. Після виправлення зазначених вище дефектів коленвали передаються на обробку шийок в ремонтні розміри.
Таблиця 2.1 Величина допустимого биття середньої корінний шийки щодо крайніх для перешлифовки в останній ремонтний розмір без правки
вихідний размервелічіна допустимого биття, в мм Р00,90Р10,65Р20,40Р30,15 Як правило для шліфування застосовується кругло-шліфувальний верстат, призначений для обробки колінчастих валів. При необхідності на таких верстатах може виконуватися шліфування галтелів колінчастого вала. Однак при шліфуванні азотованих колінчастих валів з високою міцністю шийок колінчастого вала відбувається прискорений витрата шліфувального круга. Після виконання операції шліфування і наступної операції прочищення каналів колінчастого вала слід виконати операцію динамічного балансування колінчастого вала. Операція виконується на спеціальному стенді для динамічного балансування колінчастих валів. Потім на цьому ж стенді балансується колінчастий вал в зборі з маховиком. При необхідності при цьому для досягнення відсутності дисбалансу колінчастого вала в зборі з маховиком виконуються відповідні свердління в поверхні маховика (відступивши 2,5-3 см від його вінця). Далі на цьому стенді балансується колінчастий вал в зборі з маховиком і корзиною зчеплення. При необхідності, для досягнення відсутності дисбалансу клонували в зборі з маховиком і корзиною зчеплення, виконуються відповідні свердління в поверхні зчеплення. Слід зазначити, що ці отвори не повинні бути наскрізними. 2.2 Наплавлення Наступним видом дефекту є знос шийки носка і хвостовика колінчастого вала. Найчастіше дефект усувається шляхом наплавлення і подальшої шліфовки. Також наплавка може бути застосована при відновленні шийок колінчастого вала. У цьому випадку після наплавлення поверхню необхідно піддати зміцнення. Наплавлення є нанесення за допомогою зварювання шару металу на поверхню виробу. Наплавлення дозволяє отримувати деталі з поверхнею, що відрізняється від основного металу, наприклад жаростійкістю і жароміцних, високу зносостійкість при нормальних і підвищених температурах, корозійну стійкість і т.п. Наплавлення може проводитися як при виготовленні нових деталей, так і в ремонтно-відновлювальних роботах, істотно подовжуючи термін експлуатації деталей і вузлів, забезпечуючи цим високий економічний ефект. При відбудову, ремонт наплавку виконують приблизно тим же металом, з якого виготовлено виріб, однак таке рішення не завжди доцільно. Іноді при виготовленні нових деталей (і навіть при ремонті) доцільніше на поверхні отримати метал, що відрізняється від металу деталі. Наплавлення здійснюють нанесенням розплавленого металу на поверхню виробу, нагріту до оплавлення або до температури надійного змочування рідким наплавленим металом. Наплавлений шар утворює одне ціле з основним металом (металева зв'язок). При цьому, як правило (крім деяких випадків ремонтної наплавлення, яка застосовується для відновлення початкових розмірів деталей), хімічний склад наплавленого шару може значно відрізнятися від складу основного металу. Товщина наплавленого металу, утвореного одним або декількома шарами, може бути різною 0,5 ... 10 мм і більше. Існують різноманітні способи наплавлення: Ручна дугова електродами зі стрижнями і покриттями спеціальних складів. Автоматична наплавка під флюсом. Електроди можуть бути суцільного перетину і порошкові. Склад флюсу, метал електрода і складу наповнювача визначають властивості наплавленого шару. Наплавлення плавкими і не плавляться електродами в середовищі захисних газів. Властивості наплавленого шару залежать від матеріалу присадки або електрода. Плазмова наплавка. Дуга може бути як прямого, так і непрямого впливу. Можна плазмовим струменем оплавлятися шар легованого порошку, попередньо нанесений на поверхню деталі. Електрошлакове, електронно-променева, лазерна наплавка, а також наплавлення газокисневого полум'я. У хвостовику колінчастого вала зустрічається дефект - тріщина. Зазвичай це наслідок обриву болтів маховика. У цьому випадку також застосовується метод ремонту - наплавка, можливо і завтуліваніе. При завтуліваніі шийка колінчастого вала в місці тріщини шліфується на глибину 1,5-2 мм, виготовляється кільцева обойма для посадки внатяг на зашліфоанное місце. Посадка в натяг здійснюється шляхом розігріву обойми і одночасному охолодженні хвостовика колінчастого вала. Після установки і охолодження обойми, проводиться операція шліфування до номінального розміру 104,860 ... 105,000 мм. 2.3 Електрохімічний метод обробки Електроерозійна обробка заснована на виривання частинок матеріалу з поверхні імпульсом електричного розряду. Якщо задано напруга (відстань) між електродами, зануреними в рідкий діелектрик, то при їх зближенні (збільшенні напруги) відбувається пробій діелектрика - виникає електричний розряд, в каналі якого утворюється плазма з високою температурою. Так як тривалість використовуваних в даному методі обробки електричних імпульсів не перевищує 0,1 c, що виділяється тепло не встигає поширитися в глиб матеріалу і навіть незначної енергії виявляється досить, щоб розігріти, розплавити і випарувати невелика кількість речовини. Крім того, тиск, що розвивається частками плазми при ударі об електрод, сприяє викиду (ерозії) не тільки розплавленого, але і просто розігрітого речовини. Оскільки електричний пробій, як правило, відбувається по найкоротшому шляху, то, перш за все, руйнуються найближче розташовані ділянки електродів. При наближенні одного електроду заданої форми (інструменту) до іншого (заготівлі) поверхня останнього набуде форми поверхні першого. Продуктивність процесу, якість одержуваної поверхні в основному визначаються параметрами електричних імпульсів (їх тривалістю, частотою проходження, енергією в імпульсі). Електроіскрові методи особливо ефективні при обробці твердих матеріалів і складних виробів. При обробці твердих матеріалів механічними способами великого значення набуває знос інструменту. Інструментом в електроіскровий обробці є тонка дріт, яка є дешевшою порівняно з інструментом для механічної обробки. Наприклад, при виготовленні деяких типів штампів механічними способами більше 50% технологічної вартості обробки складає вартість використовуваного інструменту. При обробці цих же штампів електроерозійними методами вартість інструменту не перевищує 3,5%. Робочі рідини повинні відповідати таким вимогам: забезпечення високих технологічних показників ЕЕО; термічна стабільність фізико-хімічних властивостей при впливі електричних розрядів з параметрами, відповідними що застосовуються при електроерозійної обробці; низька корозійна активність до матеріалів ЕІ і оброблюваної заготовки; висока температура спалаху і низька випаровуваність; хороша фільтрованість; відсутність запаху і низька токсичність. При електроерозійної обробці застосування отримали низькомолекулярні углеводородістие рідини різної в'язкості; вода і в незначній мірі кремнийорганические рідини, а також водні розчини двоатомних спиртів. Для кожного виду ЕЕО застосовують робочі рідини, що забезпечують оптимальний режимобробки. На чорнових режимах рекомендується застосовувати робочі рідини з в'язкістю (суміш гас-масло індустріальне), а на чистових (гас, сировина вуглеводневу). Електроди-інструменти (ЕІ) повинні забезпечувати стабільну роботу у всьому діапазоні робочих режимів ЕЕО і максимальну продуктивність при малому зносі. Електроди-інструменти повинен бути достатньо жорстким і протистояти різних умовмеханічної деформації (зусиллям прокачування РЖ) і температурних деформацій. На поверхні ЕІ не повинно бути вм'ятин, тріщин, подряпин і розшарування. Поверхня ЕІ повинна мати шорсткість При обробці вуглецевих, інструментальних сталей і жароміцних сплавів на нікелевій основі використовують графітові та мідні ЕІ. Для чорнової ЕЕО заготовок з цих матеріалів застосовуються ЕІ з алюмінієвих сплавів і чавуну, а при обробці отворів - ЕІ з латуні. При обробці твердих сплавів і тугоплавких матеріалів на основі вольфраму, молібдену та ряду інших матеріалів широко застосовують ЕІ з композиційних матеріалів, так як при використанні графітових ЕІ не забезпечується висока продуктивність через низьку стабільності електроерозійного процесу, а ЕІ з міді мають великий знос, що досягає десятка відсотків, і високу вартість. Знос ЕІ залежить від матеріалу, з якого він виготовлений, від параметрів робочого імпульсу, властивостей РЖ, площі оброблюваної поверхні, а також від наявності вібрації. На вибір матеріалу і конструкції ЕІ істотний вплив роблять матеріал заготовки, площа оброблюваної поверхні, перед тим як її форми, вимоги до точності і серійності вироби. За призначенням (як і металорізальні верстати) розрізняють верстати універсальні, спеціалізовані і спеціальні, по необхідної точності обробки - загального призначення, Підвищеної точності, прецизійні. Спільними для всіх верстатів вузлами є пристрій для кріплення і переміщення інструменту (заготовки), гідросистема, пристрій для автоматичного регулюванняміжелектродного проміжку (між заготівкою і інструментом). Генератори іскрових імпульсів виготовляються, як правило, окремо і можуть працювати з різними верстатами. Основні відмінності пристроїв для переміщення інструменту (заготовки) в електроерозійних верстатах від таких в металорізальних верстатах - відсутність значних силових навантажень і наявність електричної ізоляції між електродами. Гідросистема складається з ванни з робочою рідиною(Вода, гас і т.п.), гидронасоса для похитування рідини через міжелектродний проміжок і фільтрів для очищення рідини, що надходить в насос, від продуктів ерозії. Метод електроконтактні обробки. Заснований на локальному нагріванні заготовки в місці контакту з електродом-інструментом і видаленні розм'якшеного або навіть розплавленого металу із зони обробки механічним способом: відносним рухом заготовки та інструменту. Джерелом теплоти в зоні обробки служать імпульсні дугові розряди. Електроконтактні обробку опалювальному рекомендують для обробки великих деталей з вуглецевих і легованих сталей, чавуну, кольорових сплавів, тугоплавких і спеціальних сплавів. Метод застосовують при зачистці виливків від заток, відрізку літників і прибутків, зачистці прокату з спецсплавів, чорновому круглому зовнішньому, внутрішньому і плоскому шліфуванні корпусних деталей машин з важкооброблюваних сплавів, шліфуванні з одночасною поверхневою загартуванням деталей з вуглецевих сталей. Метод обробки не забезпечує високої точності і якості поверхні, але дає високу продуктивність знімання металу внаслідок використання великих електричних потужностей. Електроконтакта обробка заснована на введенні в зону механічної обробки електричної енергії - порушення потужної дуги змінного або постійного струму між, наприклад, диском, службовцям для видалення матеріалу із зони обробки, і виробом. Переваги методу - висока продуктивність (до 106мм3 / хв) на грубих режимах, простота інструменту, робота при відносно невеликих напругах, низькі питомі тиску інструменту - 30-50 кг / м2 (0,3-0,5 кгс / см2) і, як наслідок, можливість використання для обробки твердих матеріалів інструменту, виготовленого з відносно м'яких матеріалів. До недоліків відносять: велику шорсткість обробленої поверхні, теплові впливу на метал при жорстких режимах. Електроконтакта обробка не забезпечує високої точності і якості поверхні (шорсткість поверхні близько 50 мкм), але призводить до високої продуктивності внаслідок значного знімання металу. Застосовується вона для різання заготовок, обдирання відливок, заточування інструменту, плоского шліфування, прошивки отворів, очищення від окалини, обробки криволінійних поверхонь т. Д. Рекомендується для обробки вуглецевих і легованих сталей, чавуну, кольорових сплавів, тугоплавких, важкооброблюваних і спеціальних сплавів. Різновидом електроконтактні обробки є електроабразівная обробка - обробка абразивним інструментом (в т. Ч. Алмазно-абразивним), виготовленим на основі провідних матеріалів. Введення в зону обробки електричної енергії значно скорочує знос інструменту. 2.4 Термічна обробка Загартуванням ТВЧ (рис. 1.2.1.) Називають вид термічної обробки, при якому сталь нагрівають до певної температури, витримують при цій температурі, а потім швидко охолоджують в закалочной середовищі (вода, масло, солоні і полімерні рідини). Мал. 1.2.1 Схема індукційного нагріву Деталь, 2 - індуктор В результаті гарту змінюються структура і властивості стали. Основними параметрами гарту є температура нагріву, частота і швидкість охолодження. Мал. 1.2.2 Зміна проникнення струму в провідник, в залежності від частоти струму Температура гарту визначається по діаграмі оптимальних інтервалів гартівних температур вуглецевих сталей. Швидкість нагріву залежить від теплової потужності нагрівальної установки, хімічного складу стали, маси і розмірів гартованих виробів. Час нагріву складається з двох величин: часу нагріву до заданої температури і часу витримки при цій температурі. Мал. 1.2.3 Розподіл температури по перетину деталі Активний нагрів за допомогою струму, нагрів внаслідок теплопровідності, хк - товщина загартованого шару Індукційна гарт має гнучкість застосування завдяки ряду змінних параметрів і можливості індивідуального підходу до кожної деталі, що дозволяє отримувати необхідну твердість і глибину загартованого шару деталі. Переваги та економічний ефект індукційного загартування. Загартування ТВЧ забезпечує високу якість виробів і дає найбільш стабільні результати в порівнянні з іншими методами поверхневого зміцнення (великий опір зношування і втомного руйнування, малі деформації, майже повна відсутність окислення і зневуглецювання). Завдяки нагріванню тільки поверхневих шарів зменшуються витрати енергії на нагрів. Головна перевага індукційного нагріву полягає у виділенні теплоти безпосередньо в самому металі. При індукційному нагріванні струмами високої частоти реалізується можливість значної концентрації електричної енергії в невеликому обсязі нагрівається металу, що дозволяє здійснювати нагрів з великою швидкістю. даний видповерхневого зміцнення дозволяє виготовляти деталі з дешевої вуглецевої сталі, забезпечуючи їй високі характеристики. 2.5 Хіміко-термічна обробка Азотування, насичення поверхні металевих деталей азотом з метою підвищення твердості, зносостійкості, межі втоми і корозійної стійкості. Азотування сталі відбувається при t 500-650 ° С в середовищі аміаку. Вище 400 ° С починається дисоціація аміаку по реакції NH3 >> 3H + N. Утворився атомарний азот дифундує в метал, утворюючи азотисті фази. При температурі азотування нижче 591 ° С азотований шар складається з трьох фаз (рис. 1.1.1.): E - нітриду Fe2N, g "- нітриду Fe4N, a - азотистого фериту, що містить близько 0,01% азоту при кімнатній температурі. При температурі азотування 600-650 ° С можливе утворення ще й g-фази, яка в результаті повільного охолодження розпадається при 591 ° C на евтектоід a + y1. Твердість азотированного шару збільшується до HV = 1200 (відповідає 12 Гн / м2) і зберігається при повторних нагревах до 500-600 ° C, що забезпечує високу зносостійкість деталей при підвищених температурах. азотированного стали значно перевершують по зносостійкості цементовані і загартовані стали. Азотування - тривалий процес, для отримання шару товщиною 0,2-0,4 мм потрібно 20-50 годин . Підвищення температури прискорює процес, але знижує твердість шару. для захисту місць, що не підлягають азотуванню, застосовуються лудіння (для конструкційних сталей) і нікелювання (для неіржавіючих і жароміцних стале й). Для зменшення крихкості шару А. жароміцних сталей інколи ведуть в суміші аміаку і азоту. Висновки по розділу Таким чином із завданням видалення зміцненого азотированного шару можна впоратися впровадженням електрохімічного методу обробки. Оскільки при цьому методі не відбувається безпосереднього контакту електрод инструм з оброблюваної поверхнею, знос інструменту буде мінімальний, до того ж ціна витратних матеріалів в рази нижче вартості абразивного круга, що застосовується при перешліфовуванні колінчастого вала. З проблемою відсутності зміцненого шару при зменшенні азотированного шару на 0,5 мм і більше можна боротися застосувавши перевірений метод індукційного загартування. Швидка швидкість процесу загартування і відносна дешевизна методу дадуть помітний економічний ефект від впровадження методу. До того ж існує можливість перейняття досвіду ТОВ «ИНТЕРМ», описаного в першому розділі. азотований колінчастий вал двигун 3.1 Видалення азотированного зміцненого шару колінчастого вала КАМАЗ електрохімічним методом Відомий спосіб електроерозійного шліфування тіл обертання (Розмірна електрична обробка металів: Навч. Посібник для студентів вищих навчальних закладів /Б.А. Артамонов, А. Л. Вишницький, Ю.С. Волков, А.В. Глазков. / Под ред. А.В . Глазкова. - М .: Вища школа, 1978. - 336 с.), при якому електроду-заготівлі задають обертання, до нього підводять на певну відстань електрод-інструмент, між електродами подають струмінь мінерального масла і до електродів подають імпульси технологічного струму ( амплітудні значення напруги підтримуються на рівні від 20 до 200 В, струму від 10 до 50 А при частоті імпульсів до 100 кГц). При цьому до інструменту підключають мінусовій висновок генератора імпульсів. Даного способу електроерозійного шліфування тіл обертання притаманні такі недоліки: потрібна підтримка певного зазору між електродами; невисокий ККД способу, тому що процес шліфування припиняється при короткому замиканні електродів і при збільшенні зазору між електродами понад пробивний величини. На малюнку 3.1.1. представлена принципова схема пристрою для реалізації запропонованого способу. Пристрій містить джерело живлення постійного струму 1, генератор імпульсів 2, автотрансформатор 3, пристрій для подачі масла 4, електрод-інструмент 5 і електрод-заготовку 6. Спосіб здійснюється наступним чином. Оброблювана електрод-заготовка 6 підключається до позитивного полюса автотрансформатора 3, а електрод-інструмент 5 - до негативного полюса. Первинна обмотка автотрансформатора 3 харчується від джерела живлення постійного струму 1, а імпульси струму створюються генератором імпульсів 2, який включений послідовно до первинної обмотці. Електрод-заготовка 6 приводиться в обертання, до неї підводиться електрод-інструмент 5, до якого прикладається зусилля, що забезпечує питомий тиск в контакті до 0,5 МПа. Між електродами подається масло через пристрій 4, після чого включається джерело живлення 1. Генератор імпульсів 2 перетворює постійний струмв імпульсний з частотою імпульсів до 100 кГц, амплітудні значення напруги за допомогою автотрансформатора 3 варіюються в межах від 1 до 50 кВт, що забезпечує силу імпульсного струму в контакті електрода-заготовки 6 і електрод-інструмента 5 в межах від 1 мкА до 100 мА. Мал. 3.1.1 Принципова схемаобробки поверхні Шліфування циліндричної електрод-заготовки, виготовленої зі сталі 45, електродом-інструментом з БрОЦС-4-4-4 при частоті імпульсів напруги 100 кГц, амплітудних значеннях напруги між електродом-заготовкою і електродом-інструментом 10 кВт протягом 0,1 год забезпечує зняття шару 0,2 мм. Шорсткість обробленої поверхні електрода-заготовки 0,1 мкм при початковій 0,63 мкм. При шліфуванні між електродом-заготовкою і електродом-інструментом подавалося мінеральне масло М8Г2К, а питомий тиск в контакті досягало 0,5 МПа. Спосіб 2. «Пристрій для електрохімічної обробки шийок колінчастого вала» Патент 2157744, автори: Милих В.А .; Захаров І.С. Відомо "Пристрій для електролітичного очищення металевих поверхонь" (АС СРСР N 753931 від 07.08.80, C 25 F 7/00), що містить рухливий електрод, виконаний у вигляді гнучкої пластини, ущільнення з ізолюючого матеріалу, закріплене по периметру електрода, що фіксують елементи з діелектричного матеріалу і штуцери для підведення і відведення електроліту. Недоліком цього пристрою є недостатня точність розмірної обробки, низька продуктивність процесу. Відомо "Пристрій для розмірної електрохімічної обробки довгомірних нежорстких деталей" (АС СРСР N 1618536 від 07.01.91, В 23 H 3/00), що містить що розміщується на оброблюваній ділянці локальну заповнену електролітом камеру для електрохімічної обробки, в якій встановлений електрод-інструмент, привід обертання оброблюваного вала, джерело технологічного струму, а також державка з двома завзятими фланцями, в пазах яких встановлена з можливістю поперечного переміщення камера. Цьому пристрою притаманні такі недоліки: складність пристрою в разі обробки циліндричних шийок колінчастого вала; необхідність стежить механізму, що забезпечує необхідний міжелектродний зазор; складність розміщення пристрою між щоками противагами; низька продуктивність через неможливість одночасної обробки декількох шийок. Найбільш близьким аналогом розглянутого пристрою є пристрій для електрохімічної обробки шийок колінчастого вала (RU 2043884, МПК 7 B 23 H 9/04, 20.09.1995) (рис. 3.1.2.), Що містить роз'ємну камеру для електрохімічної обробки, встановлений в ній електрод -Інструмент з струмопідведення, колектори для підведення і відведення електроліту, а також джерело струму. Технічно характеристики пристрою є пристрій для електрохімічної обробки шийок колінчастого вала: Чисте час обробки клонували 5-15 хв Кількість оброблюваних колінчастих валів в зміну до 8 Оброблювані шийки корінні і шатунні одночасно Споживана потужність електроенергії 2 КВт / год Необхідне приміщення для верстата 0 м.кв Робоча напруга на електродах 3-16 В Частота пульсацій 100 Гц Кількість вихідних каналів 20 Максимальна сила струму на 1 каналі 10 А Робочий зазор при обробці 0,1-0,5 мм Інтенсивність знімання 0,5 мм / хв Концентрація електроліту 10-30% Діаметр обративаемих шийок 15-120 мм Точність обробки 0,001 мм Частота обертання деталі 10-20 об / хв Витрата електроліту 10-15 л / хв; Ширина оброблюваних шийок до 120 мм Спосіб регулювання безперервно Тип струму пульсуючий Сигналізація закінчення світлова Закінчення обробки автоматичне від датчика Відключення робочої напруги автоматичне Електроліт водний розчин NaCl Цей пристрій також притаманні недоліки, зазначені вище. Завданням розробки є розширення технологічних можливостей пристрою за рахунок інтенсифікації процесу обробки шляхом додання електроду-інструменту обертального руху. Завдання вирішується тим, що пристрій містить роз'ємну по довжині камеру для електрохімічної обробки з встановленим в ній електродом-інструментом з струмопідведення, колектори для підведення і відведення електроліту і джерело струму. Камера виконана циліндричної з можливістю її коаксіальної установки на оброблювану ділянку, на її внутрішній стінці, зверненої до валу, виконані рівномірно по довжині камери кільцеві канавки, всередині яких виконані рівномірно по окружності тангенциально розташовані отвори для підведення в порожнину камери електроліту і приводу в обертання електрода інструменту, причому отвори в сусідніх канавках зрушені один щодо одного на заданий крок, електрод-інструмент виконаний порожнистим циліндричним, встановлений з можливістю обертання і охоплення оброблюваної ділянки вала і складається з двох кільцевих фланців, з'єднаних між собою рядом концентрично розташованих по колу осей, при цьому фланці складаються з окремих сегментів, скріплених по сполучаються площин, на зовнішній стороні осей розміщені рядами по числу канавок камери пружні струмопідведення, скріплені з осями і розташовані рівномірно по колу з можливістю контакту і переміщення по ним, причому кожен ряд то коподводов зрушать один щодо одного на заданий крок, кратний кроку осей, на внутрішній стороні осей по всій їх довжині розташовані скріплені з ними робочі кромки електрода-інструменту, виконані у вигляді гнучкої несучої пластини, прилеглі до ділянок поздовжнього контуру оброблюваної ділянки вала і забезпечені обмежувачами для створення межелектродного зазору. Гнучка несуча пластина забезпечена скріпленими з нею смугами з струмопровідної тканини, наприклад вуглеволокна, що лежать на жорсткому пружному ворсі з неелектропровідних волокна. Пристрій для електрохімічної обробки включає монтажну плату з елементами з'єднання її з оброблюваною ділянкою клонували - шатунной шийкою, розташованої між щоками противаг. Монтаж і кріплення пристрою здійснюється через діелектричну прокладку за допомогою шпильок, вкручених в глухі нарізні заглушки з діелектричного матеріалу, монтовані в різьбові отвори системи змащення вкладишів коленвала. Пристрій містить циліндричну камеру електрохімічної обробки з кільцевих колектором підведення електроліту в зону обробки, рухливий обертається електрод-інструмент, роз'ємний кожух камери зливу електроліту з фланцями, виконаними з діелектричного матеріалу. Коаксиальная установка камери електрохімічної обробки щодо оброблюваної шатунной шийки забезпечується базуванням монтажної плати пристрою щодо циліндричних поверхонь поруч розташованих корінних шийок коленвала - цим досягається однаковий міжелектродний зазор. Внутрішня, звернена до оброблюваної поверхні стінка камери містить діелектричне покриття, прорізаний до металу кільцевими канавками, рівномірно розташованими по всій довжині камери. У канавках рівномірно по колу виконані тангенціальні отвори, що з'єднують кільцевої колектор підведення електроліту з камерою. Для зменшення пульсації тиску в міжелектродному зазорі через дискретного розташування отворів отвори в сусідніх канавках зрушені один щодо одного із заданим кроком. Для забезпечення монтажу камери навколо оброблюваної шийки камера виконана рознімної з поздовжнім стиком, а її коаксіальне розташування забезпечується конструкцією кільцевого колектора, що включає внутрішню посадкову поверхню і гвинтове з'єднання роз'єму. Монтажна плата, верхня частина колектора і штуцер підведення електроліту створюють жорстку опорну конструкцію, яка служить для точної установки пристрою щодо оброблюваної поверхні, і є основою для кріплення кожуха ванни зливу електроліту. Нижня частина колектора і нижня частина кожуха ванни зливу електроліту забезпечують складання і коаксіальну установку камери навколо шийки колінчастого вала. Корпус рухомого обертового електрода-інструменту рознімною конструкції, що складається з декількох пружних сегментів, виконаний у вигляді порожнистої циліндричної конструкції типу "білячого колеса", що охоплює шийку вала. Її основу складають два кільцевих фланця, з'єднаних між собою рядом концентрично розташованих по колу осей. Зовнішня і торцева поверхня фланців має діелектричне покриття. Кожен сегмент з'єднаний торцевими площинами за допомогою пружин зв'язку. На зовнішній поверхні корпусу розташовані пружні струмопідведення, скріплені з осями і розташовані рівномірно по периметру окружності перетину електрода і контактують з канавками камери. Кожен ряд токоподводов, по числу канавок, зрушать один щодо одного на певний заданий крок, кратний кроку осей, забезпечуючи рівномірне поджатие і, отже, однаковий міжелектродний зазор. У початковому стані пружини, що з'єднують окремі сегменти корпусу електрода-інструменту, розширюючись взаємно, підтискають зовнішню поверхню з токоподводами до внутрішньої стінки камери, забезпечуючи надійний електричний зв'язок рухомого електрода-інструменту. На внутрішній поверхні корпусу електрода, зверненої до оброблюваної поверхні, розташовані робочі формотворчих кромки. Вони виконані у вигляді гнучкої несучої пластини, скріпленої з осями і прилеглими в процесі обробки по всій довжині шийки вала. Причому для забезпечення постійного міжелектродного зазору вони забезпечені обмежувачем із діелектричного матеріалу. Таким чином, коаксіальна установка рухомого електрода забезпечується контактом пружних токоподводов з камерою і гнучких несучих пластин з валом. Робочі формотворчих кромки можуть бути виконані у вигляді гнучкої несучої пластини і скріплених з нею, вільно лежать на жорсткому пружному ворсі з неелектропровідних волокна смуг з струмопровідної тканини, наприклад, на основі вуглецевого волокна. Пристрій працює наступним чином. Вимагає чистової обробки після ремонту наплавленням шатунних (корінних) шийок колінчастий вал встановлюється горизонтально. Пристрій монтується за допомогою монтажної плати на щоках противаг колінчастого вала. Для цієї мети вивертають різьбові пробки в сусідніх щоках противаг і замість пробок вворачивают заглушки з діелектричного матеріалу, забезпечені шпильками. Необхідно зауважити, що, так як колінчастий вал має канали системи мастила, що проходять в тілі корінних і шатунних шийок, то необхідно перед обробкою герметизувати отвори, що виходять на поверхню шийок. Для підготовки пристрою до роботи його попередньо розбирають по поздовжніх стиків. Спочатку відокремлюють нижню частину кожуха ванни зливу електроліту. Потім знімають нижню половину кільцевого колектора підведення електроліту, вивертаючи гвинти стику. Після цього камера електрохімічної обробки розділяється на дві частини. Корпус електрода-інструменту роз'єднують за місцем стику і монтують біля шийки вала, знову поєднуючи сегменти корпусу. Після цього виставляють монтажну плату щодо сусідніх корінних шийок колінчастого вала. Для цього за допомогою настановних шайб, затягуючи гайки шпилькових з'єднання, забезпечують необхідну установку монтажної плати, контролюючи правильність установки за допомогою вимірювального інструмента, наприклад індикатора годинного типу. Далі все пристрій монтують в зворотній послідовності, тобто з'єднують дві половини рознімної камери, перевіряючи, щоб пружні струмопідведення увійшли в канавки камери. Потім приєднують нижню частину колектора підведення електроліту. Після цього монтують нижню частину кожуха ванни зливу електроліту. Під'єднують до штуцерів підведення і відведення електроліту трубопроводи. На цьому складання пристрою закінчується. При подачі електроліту під тиском через штуцер, виконаний в монтажній платі, рідина проходить в кільцевої колектор і через тангенціальні отвори рівномірно розподіляється по всій поверхні оброблюваної шийки колінчастого вала. За рахунок турбулентного вихрового руху електроліт притискає струмопровідну тканину до жорсткого ворсу, створюючи стабільність умов обробки. Через торцеві зазори між корпусом електрода-інструменту і щоками противаг електроліт зливається в кожух ванни. Підведення технологічного струму до електрода-інструменту здійснюється через пружні струмопідведення. В якості приводу обертання електрода-інструменту в пристрої використовується енергія подається під тиском електроліту. Пружні струмопідведення, розташовані на зовнішній поверхні корпусу електрода-інструменту, в цьому випадку, крім свого основного призначення - підведення струму, виконують роль лопаток робочого колеса гідротурбіни, на яких енергія рідини переходить в енергію обертання. В результаті всебічного тиску на пружні струмопідведення і зовнішню поверхню електрода-інструменту стискаються пружини зв'язку сегментів корпусу. І, отже, робочі формотворчих кромки електрода наближаються до оброблюваної поверхні шийки колінчастого вала. Обертання електрода-інструменту в камері дозволяє інтенсифікувати процес електрохімічної обробки за рахунок швидкого відведення продуктів реакції і постійного оновлення електроліту у оброблюваної поверхні. В процесі анодного розчинення знімається верхній шар металу рівномірно по всій поверхні. Наявність обмежувальних елементів дозволяє витримати постійний міжелектродний зазор і запобігає можливість коротких замиканьі підгоряння поверхні і робочих крайок. Виконання робочих крайок електрода у вигляді гнучкої несучої пластини і вільно розташованих по всій довжині оброблюваної поверхні смуг з струмопровідної тканини, наприклад на основі вуглеволокна, і використання в якості обмежувача ворсу з неелектропровідних волокна дозволяє інтенсифікувати процес анодного розчинення за рахунок прилягання робочих крайок по більшій ділянці поверхні і підвищити якість обробки за рахунок усунення пористої структури (смугастості поверхні) і виключення коротких замикань. У міру анодного розчинення збільшується міжелектродний зазор за рахунок зменшення діаметра шийки колінчастого вала. Після досягнення необхідного діаметра вимикають технологічний ток і подачу електроліту. Незважаючи на деяке ускладнення пристрою в порівнянні з прототипом, пропоноване технічне рішення має ряд переваг, які забезпечують позитивний ефект, а саме: можливість використання в умовах ремонтних органів при відсутності складного верстатного обладнання для шліфування та суперфінішне обробки шийок колінчатих валів; зменшення трудомісткості технологічного процесу і підвищення чистоти поверхні за рахунок інтенсифікації процесу анодного розчинення шляхом додання обертального руху електроду і вирівнювання процесу розчинення по всій поверхні; підвищення продуктивності за рахунок одночасної обробки декількох шийок колінчастого вала одночасно. Таким чином в розширенні технологічних можливостей пристрою за рахунок інтенсифікації процесу обробки шляхом додання електроду-інструменту обертального руху виражений позитивний ефект пропонованої конструкції. 3.2 Индукционная гарт струмами високої частоти Зміцнення колінчастого вала в ВАТ «КАМАЗ-Дизель». Самостійне зміцнення з використанням установки індукційного нагрівальної. Найбільш зручним варіантом буде застосування шліфувального верстата в якості механізму обертання і окремо встанови ТВЧ, як пристрій зміцнення. В цьому випадку дуже зручний метод, впроваджений в ТОВ «Науково-технічний, освітній та виробничий центр високочастотних електротехнологій« ИНТЕРМ ». Ними розроблена технологія індукційного поверхневого гарту ТВЧ з використанням токарного верстата в якості приводу обертання і переміщення. Типовий шліфувальний верстат в описі не потребує. Розглянемо докладніше установку ТВЧ виробництва ТОВ НКВП "Петра": Установка індукційна нагрівальна ПЕТРА-0501 (рис. 3.2.1.) Широко застосовується для оснащення термічних ділянок в технологіях: індукційна пайка (в т.ч. пайка різців), ТВЧ-гарт валів, шестерень, нагрів під штампування решт заготовок. Вона ефективно замінює собою лампові ТВЧ-установки типу ЛЗ і ВЧГ. У порівнянні з ламповими установками ПЕТРА-0501 має високий ККД, малі габарити і не вимагає додаткового часу перед початком і після закінчення роботи на розігрів і охолодження лампи. Порівняно з напівпровідниковими аналогамиважливою перевагою є можливість застосування широкого набору індукторів без перемикань всередині установки, тривалість включення - 100%. високий допустимий рівеньповної потужності індуктора (до 600 кВА). Індукційний нагрів із застосуванням установок ТВЧ реалізується за рахунок енергії змінного магнітного поля. Оброблювана деталь вноситься всередину петлі індуктора необхідної величини. високочастотний змінний струм(ТВЧ), що проходить по цій петлі, індукує на поверхні деталі вихрові струми, величина яких контролюється установкою. Використання установки ТВЧ характеризується високою ефективністю перенесення енергії і малими тепловими втратами. Глибина проникнення індукованих струмів безпосередньо залежить від робочої частоти ТВЧ установки індукційного нагріву. Чим вище частота, то більша відносна щільність струму на поверхні оброблюваної деталі. Знижуючи робочу частоту на установці ТВЧ, можна збільшувати глибину проникнення струмів. Установка індукційна ТВЧ ПЕТРА-0501 має ряд переваг перед ламповими і напівпровідниковими установками. 1.Індуктор (рис. 3.2.3.) Ізольований від мережі і заземлений; 2.Широкий набір індукторів без перемикань всередині установки; .Ефективна робота на пайку і поверхневому загартуванню без перемикань всередині установки; .Нагрівальний пост легко вбудовується в технологічну лінію; .Ефективна швидкодіючий захист; Крім цього, точна локалізація енергії при використанні індукційного нагріву установкою ТВЧ визначає малу тривалість технологічного циклу, високу продуктивність, удосконалює показники використання устаткування і матеріалів, а також зменшує ризик деформації оброблюваної деталі при нагріванні. Це відбувається через те, що індукційний нагрів ТВЧ формує тепло прямо всередині деталі. Енергія майже не розсіюється навколо. Перераховані переваги визначають максимальну економічну ефективність застосування установок ТВЧ в порівнянні з іншими типами установок. Використання індукційного нагріву ТВЧ дозволяє легко керувати процесом, так як інтерфейс установки простий і не вимагає спеціальної підготовки. Крім того, при роботі установки індукційного нагріву ТВЧ не виділяється дим, токсичні речовини та ін., Процес нагріву менш небезпечний для довкілляі персоналу. 3.3 Фінішна обробка колінчастого вала КАМАЗ Після шліфування колінчастого вала, з подальшим зміцненням індукційної загартуванням ТВЧ, необхідно виконати фінішну обробку колінчастого вала. Це шліфування на шліфувальному верстаті до номінальних розмірів + 0,02-0,03 мм, суперфінішірованіе і полірування. Суперфінішування. Основна мета суперфінішування, наприклад, для шийок колінчастого вала, - створення мікропорожнин для змащення, що особливо важливо в початковий період роботи кривошипно-шатунного механізму. Це досягається за допомогою коливальних абразивних брусків, що забезпечують принцип «неповторюваного сліду». Устаткування - спеціальні верстати. Наприклад, при обробці шийок колінчастого вала на всі корінні і шатунні шийки одночасно встановлюються абразивні бруски, які вчиняють в процесі обробки подвійне рух. Установ - в центрах. Інструмент - абразивні бруски, які мають зернистість 5 ... 8 мкм. Мал. 3.3.1 Схема процесу суперфінішування Схема обробки деталі Суперфінішування зображена на рис. 3.3.1. В процесі обробки бруски здійснюють зворотно-поступальний переміщення в межах 2 ... 6 мм і осцилюють з частотою v = 200 ... 1000 хв-1. При обробці застосовується охолодження гасом з добавкою 10 ... 15% веретенного масла. Середній тиск на бруски становить 0,5 ... 25 МПа. Пристрій дозволяє одночасно обробити за 20 з всі корінні і шатунні шийки колінчастого вала в наступному режимі: n = 135 хв-1, хід 5 мм, v = 450 хв-1. Головна вимога цього процесу - частота коливань v не повинна бути кратною частоті обертання n деталі, щоб забезпечувався принцип «неповторюваного сліду». Полірування. Процес полірування являє собою чистову обробку поверхні деталі м'якими колами з нанесеним на них (шаржування, наклейкою) дрібнозернистим абразивним порошком, змішаним з мастилом. Устаткування: полірувальні бабки, в масовому виробництві - полірувальні автомати. Установ: деталь тримають в руках (наприклад, при обробці лопаток компресора) або встановлюють в перехідний пристосування. Інструмент - полірувальні кола з фетру, повсті, шкіри, парусини, морської трави, капронових ниток. Шорсткість і точність - см. В таблицю. Схема процесу полірування деталей обертання зображена на рис. 3.3.2. Мал. 3.3.2 Схема полірування деталей обертання Полірування не виправляє геометричні похибки і розмір. Головна мета цього процесу - створити в результаті обробки при швидкості до 40 м / с поверхню з низькою шорсткістю, що має дзеркальний вид. 3.4 Технологічний проект ділянки ремонту колінчастих валів Підбір технологічного обладнання для ділянки ремонту колінчастих валів. Виходячи з вище наведених методик, ділянка буде обладнаний: Таблиця 3.4.1 габаритні розміриобладнання НаіменованіеКол-воГабарітние розміри, ммСтанок шліфовальний23650х2250х1800Електроерозіонний станок1967х450х1800Сварочний полуавтомат1480х275х380Пріспособленіе для редагування колінчастих валов11200х70х700Прізма11200х30х40Компрессор12030x680x1400Шкаф інструментальний21850x600x500Верстак1870x1200x700Стеллаж22000x1000x300 Уточнений розрахунок площі ділянки Висновки по розділу Розроблено спосіб видалення зміцненого азотированного шару колінчастого вала КАМАЗ Євро-2. Зміцнення колінчастого вала після шліфовки на глибину більше 0,5 мм буде проводиться індукційної загартуванням струмами високої частоти. Розроблено технологічний проект ділянки ремонту колінчастих валів КАМАЗ. ВИСНОВОК За результатами виконаного дипломного проекту стану питання ремонтопридатності колінчастого вала можна зробити наступні висновки: Основними причинами ремонту або заміни колінчастого вала є задираки шийок, зношування вище граничних значень при задирах, втомне руйнування, залишкові деформації у вигляді вигину осі, тріщини на поверхні шийок, які обумовлені завершенням процесу провертання вкладишів. Від завершення або попередження цього процесу залежить і ремонтопридатність і довговічність колінчастого вала. Слід зазначити, що вихід з ладу азотованих колінчастих валів найчастіше обумовлений недбалою експлуатацією. Часті перевантаження, наслідком якого є перегрів тертьових пар в доповненні з не якісним моторним масломпризводять до поломки двигуна. Колінчасті вали двигунів Євро-2 КАМАЗ-740 допускають ремонт перешліфовці в перший ремонтний розмір, без повторного зміцнення шийок. Моделі владишей колінчастого вала 740.60 дозволяють ремонтувати колінчастий вал зниженням товщини шийок на 0,25 мм по діаметру. Однак не глибокий зміцнений шар глибиною 0,5-0,7 мм, знижує можливість ремонтопридатності колінчастого вала при глибоких задирах, коли потрібно перешліфовка на два ремонтних розміру. А також висока твердість азотированного шару не дозволяє застосовувати звичний метод перешлифовки колінчастого вала в ремонтний розмір через підвищеної витратиабразивного круга. В випадків глибокого провороту і задирів шийок необхідно буде провести повторне зміцнення. Для вирішення цих двох ключових питань було розроблено спосіб зняття азотированного шару колінчастого вала методом електрохімічної шліфування і повторне зміцнення індукційного загартуванням струмами високої частоти. Зняття зміцненого шару проводиться електроерозійним обладнанням. Повторне зміцнення проводиться індукційної установкою в заводських умовах, або впровадженням цієї технології у власному виробництві. Робочий інструмент цих двох методів має невеликий розмір, що дає можливість застосовувати його установкою на шліфувальний верстат, це буде зручним для процесу чистового шліфування в номінальний розмір або фінішної обробки. У випадку повного не ремонтопридатності колінчастого вала існує можливість застосування колінчастих валів двигунів Євро-3 з маркуванням 740.63-1005020-10. Ці колінчаті вали упрочняются струмами високої частоти і мають в собі всі переваги колінчастих валів, зміцнених індукційної загартуванням. Однак виникають наступні питання: Перше, це поведінка колінчастого вала зміцненого ТВЧ і азотуванням одночасно, стик цих двох зміцнень доводиться на галтелі шийок. Друге питання, це залишкова міцність, тому що в разі ремонту товщина шийок зменшується, в наслідок чого перекриття корінних і шатунних шийок також зменшується, що знижує міцність на кручення. Залишається необхідним провести стендові дослідження двигуна з відремонтованим за пропонованою технологією колінчастим валом для перевірки можливості впровадження даної технології ремонту на практиці. СПИСОК ВИКОРИСТАНИХ ДЖЕРЕЛ ТА ЛІТЕРАТУРИ 1.Азаматов Р.А., Дажін В.Г., Кулаков А.Т., Модин А.І. Відновлення деталей автомобілів КамАЗ / Под ред. В.Г. Дажін. - Набережні Човни: КамАЗ, 1994. 215с. 2.Бежанов Б. Н. Пневматичні механізми. М., 1957.251 с. 3.Бєлов С.В., Ільницька А.В., Козьяков А.Ф. та ін. Безпека життєдіяльності. - Москва: Изд-во «Вища школа», 1999. -448с. 4.В.В. Петросов Ремонт автомобілів і двигунів. М. Видавничий центр Академія, 2007 г., 3-е видання. 5.Відновлення деталей машин: Довідник / Ф.І. Панте-леенко, В.П. Лялякін, В.П. Іванов, В.М.Константінов; Під ред. В.П. Іванова.-М .: Машинобудування, 2003.-672с. .відновлення зношених деталейавтоматичної вибродуговой наплавленням. Челябінськ, Кн. Вид., 1956.-207с. .Герц Є. В. Пневматичні пристрої і системи в машинобудуванні. М., 1981. .Герц Є. В., Крейнін Г. В. Розрахунок пневмоприводов. М., 1975. 271 с. 9.Гігієнічні вимоги до персональних ЕОМ та організації роботи СанПИН 2.2.2 / 2.4.1340 - 03. 10.Гідравлічне та пневматичне обладнання загального призначення, що виготовляється в СНД, Литві, Латвії. М., 1982. 123 с. 11.Гуляєв А. П. Металознавство. М., 1966. 12.Денисов А.С. Основи формування Експлутационниє-ремонтного циклу автомобілів. Саратов: Сарат. держ. техн. ун-т, 1999. 352с. 13.Доценко Г. Н. Відновлення чавунних колінчастих валів автоматичної наплавленням. М., Транспорт., 1970. 56 с. 14.Доценко Г. Н. Зносостійкість і втомна міцність чавунних колінчастих валів ГАЗ - 21, нових і відремонтованих. // Автомобільна промисловість. 1969. №2. .Доценко Н. І. Відновлення колінчастих валів автоматичної наплавленням. М., 1965. .Єгоров М. Є. Основи проектування машинобудівних заводів. М., 1969. .Єфремов В. В. Ремонт автомобілів. М., 1965. 18.ІНЕКО економічне обгрунтування ДИПЛОМНИХ ПРОЕКТІВ Методичні вказівки ДЛЯ СПЕЦІАЛЬНОСТІ 190601 «АВТОМОБІЛІ і АВТОМОБІЛЬНЕ ГОСПОДАРСТВО» Набережні Челни, 2008 р 19.КІС ГК КАМАЗ під загальним керівництвом В.М. Баруна Автомобілі КАМАЗ 6х4. Технічне обслуговування та ремонт. Керівництво. Військове видавництво МО СРСР, 1983 г. 20.Клочнев Н. І. Високо-випробувальний чавун з кулястим графітом. М., Машгиз., 1963. 21.Кування і штампування. Довідник. У 4-х т. М., 1985. Т. 2. .Краснощеков М. М., Пахомов Б. П., Марковський Є. А. Дослідження зносостійкості колінчастих валів методом радіоактивних ізотопів // Трактори і сільгоспмашини. 1962. №2. .Кудрявцев І. В. Конструкційна міцність чавуну з кулястим графітом. М., Машгиз., 1957. 25.Лугиніни. Н. Г. Технологія ремонту тепловозів, М .: «Транспорт», 1972. 26.Луппиан Р. Е., Сімонятов В. Г. Відновлення вибродуговой наплавленням в кисні чавунних колінчастих валів М - 21. // Автоматична наплавка. 1968. №4. 27.Марковський Є.А. Зносостійкість чавунів з кулястим графітом // Високоміцний чавун. Київ, 1964. .Нормативи для технічного нормування робіт при автоматичній зварці під шаром флюсу. М., 1954. 142 с. .ВАТ КАМАЗ Каталог деталей і складальних одиниць КАМАЗ-65111 з двигунами рівня Євро-1, Євро-2, Євро-3 65111-3902001КД, Набережні Челни, 2010 р 30.ВАТ КАМАЗ НТЦ Дослідження ремонтопридатність колінчастих валів двигунів КАМАЗ. Технічний звіт, Набережні Челни, 2004 р 31.ВАТ КАМАЗ Керівництво по експлуатації Двигуни КАМАЗ екологічних класів ЄВРО-2 і Євро-3 740.60-3902001 РЕ, Набережні Челни, 2009 г. 32.ВАТ КАМАЗ Керівництво по експлуатації та технічного обслуговуваннядвигунів екологічного класу Євро-3,4, 740.60-3902010РЕ, Набережні Челни 2011 р .ВАТ КАМАЗ Керівництво по експлуатації, технічного обслуговування і ремонту Двигуни КАМАЗ 740.11-240, 740.13-260, 740.14-300, 740.30-260, 740.50-360, 740.51-320, 740.50-3901001 КД, Набережні Челни, 2002 г. .Устаткування й нормативи часу для технічного нормування робіт на металорізальних верстатах, дрібносерійне і одиничне виробництво. Ч. 1. М., 1967. 315 с. .Устаткування й нормативи часу для технічного нормування робіт на шліфувальних і доводочних верстатах (укрупнені). М., 1974. 112 с. .Устаткування й нормативи часу на слюсарну обробку деталей і слюсарно-складальні роботи по збірці машин і приладів в умовах масового, великосерійного і среднесерійного типів виробництва. М., 1991. 158 с. .ОНТП-14 - 86. Норми технологічного проектування підприємств машинобудування. М., 1987. 96 с. .ОНТП-14 - 90. Норми технологічного проектування підприємств машинобудування. М., 1991. 115 с. 39.ТОВ «ИНТЕРМ» # "justify"> 40. ТОВ «ПЕТРА» # "justify"> 41. ОСТ 32 - 9 - 81 ССБТ. Норми штучного освітлення об'єктів залізничного транспорту. М., 1982. 40 с. 42.Охорона праці. Г.Ф. Денісенко.-М .: Вища школа, 1985 -319 с. 43.Полиновский Л. А. Розрахунок припусків на механічну обробку. Визначення точності обробки. Методичні вказівки до виконання лабораторних і практичних робіт. Новосиб., СГУПС. 1988. 12 с. 44.Полтев М.К. Охорона праці в машинобудуванні: Підручник. - М .: Висш.школа, 1980.-294 с., Іл. 45.Постанова головного санітарного лікаря РФ «Про введення в дію санітарних правил СП 1.1.1058-01» від 13 липня 2001 г.№ 18. 46.Розрахунок і проектування штучного освітлення виробничих приміщеньі відкритих майданчиків. Методичні вказівки до вирішення задач. Новосибірськ. 1989. 30 с. 47.Розрахунок режимів різання при механічній обробці металів і сплавів. Методичний посібник. Хабаровськ. 1997. 83 с. 48.СанПіН 2.2.4.548-96. Гігієнічні вимоги до мікроклімату виробничих приміщень. 49.Збірник типових інструкцій з техніки безпеки. М., 1994. 432 с. 50.Середенко Б. Н. Зносостійкість високоміцного чавуну, що застосовується в тракторобудуванні. // Наукові праці ін-т машинознавства і сільськогосподарської механізації. Київ, 1958. Т. 4. .СНиП 11 - 4 - 79. Природне і штучне освітлення. М., 1980. 48 .Спиридонов Н. В. Плазмові і лазерні методи зміцнення деталей машин. Мінськ, 1988. 155 с. .Хасуи А. Наплавлення та напилення. М., 1985. 239 с. .Шадрічев В.А. «Основи технології автомобілебудування і ремонт автомобілів». М., Машинобудування, 1976, 560 стор. .Артамонов Б.А., Волков Ю.С. та ін. Електрофізичні та електрохімічні методи обробки матеріалів. М .: Вища школа, 1983 .Лівшиць А.Л. Електроерозійна обробка металів. М .: Вища школа, 1979 .Артамонов Б.А. та ін. Розмірна електрична обробка металів. М .: Вища школа, 1979 .Довідник по електрохімічним і електрофізичних методів обробки. Під ред. Волосатова В.А. Ленінград: Машинобудування, 1988 .Немилов Е.Ф. Електроерозійна обробка матеріалів, Л., Машинобудування, 1989 .Фатєєв Н.К. Технологія електроерозійної обробки, Л., Машинобудування, 1990. .Артамонов Б.А., Волков Ю.С. та ін. Електрофізичні та електрохімічні методи обробки матеріалів М .: Вища школа, 1983 .Дріц М.Є., Москальов М.А., Технологія конструкційних матеріалів і матеріалознавство. М .: Вища школа, 1990. .Дальський А.М. Технологія конструкційних матеріалів. М .: Машинобудування, 2002
ВСТУП .. 2
1. Загальний пристрій і технічна характеристика двигуна КамАЗа 740.10 3
2. Пристрій кривошипно-шатунного механізму. 5
3. Розбирання, ремонт і збірка шатунно-поршневої групи.. 15
ВИСНОВОК .. 23
Список використаних джерел ... 24
ВСТУП
Акціонерне товариство (АТ) КамАЗ випускає автомобілі з колісними формулами 6x4, 4x2 і 6x6, що розрізняються потужностними, розмірними та ваговими параметрами. Масове виробництво автомобілів сімейства КамАЗ і їх надходження в автотранспортний комплекс країни почалося в 1976 р Під час виробництва удосконалювалася конструкція автомобілів та їх складових частин, підвищувалася їхня якість, накопичувався і вивчався передовий досвід експлуатації і ремонту.
У цій роботі докладно описана конструкція кривошипно-шатунного механізму в двигуни 740.10 автомобіля КамАЗ. Технічна характеристика двигуна приведена в табл.1. За своїми екологічними показниками двигун 740.10 відповідають вимогам правил ЄЕК ООН рівня EVRO-2. Наведено всі необхідні рекомендації заводу-виготовлювача по регулювань двигуна і його систем, основних несправностей, методам їх виявлення і усунення.
Метою курсової роботи є вивчення будови кривошипно-шатунного механізму двигуна КамАЗа 740.10
1. Загальний пристрій і технічна характеристика двигуна КамАЗа 740.10
На автомобілях КамАЗ встановлюються восьмициліндрові, V-образні, чотиритактні дизелі моделі 740 з рідинним охолодженням.
Блок-картер двигуна відлитий з чавуну і знизу закритий штампованим піддоном. У розточеннях блоків встановлені гільзи циліндрів «мокрого» типу. Зверху гільзи закриті індивідуальними головками. Механізм газорозподілу верхнеклапанний. У нижній частині розвалу блоку передбачати розподільний вал. Під ним у корінних опорах - колінчастий вал.
У передній частині блоку з колінчастим валом установлена гидромуфта приводу вентилятора. З правого боку блоку кріпляться відцентровий фільтр очищення масла, масляний фільтр, Маслозаливная горловина і щуп для контролю рівня масла в піддоні. З лівого боку нижньої частини блоку встановлений електростартер.
Із зовнішнього боку бічних поверхонь головок циліндрів кріпляться випускні трубопроводи, з внутрішньої сторони - впускні трубопроводи і водовідвідні труби. Зверху до впускних трубопроводах кріпиться фільтр тонкого очищення палива. На передніх кінцях водовідвідних труб встановлені термостати системи охолодження двигуна.
У розвалі блок-картера розміщені паливний насос високого тиску, Компресор і насос гідропідсилювача рульового управління.
Зазначені конструктивні рішення, а також застосування автоматичної гідромуфти в приводі вентилятора і двох термостатів в системі охолодження, ефективна очистка масла, палива і повітря забезпечують високу довговічність деталей і вузлів двигуна.
Основні параметри двигуна моделі 740.10 наведені в технічною характеристикою(Табл.1)
Таблиця 1.
Технічна характеристика
Модель двигуна | 740.10 |
Тип двигуна | З запалюванням від стиснення |
число тактів | Чотири |
число циліндрів | Вісім |
Розташування циліндрів | V-подібне |
кут розвалу | 90 ° |
Порядок роботи циліндрів | 1-5-4-2-6-3-7-8 |
Діаметр циліндра і хід поршня, мм | 120x120 |
Робочий об'єм, л | 10,85 |
Номінальна потужність брутто, кВт (к. С) | 176(240) |
Максимальний крутний момент брутто.Н. м (кгс. м) | 833(85) |
Частота обертання колінчастого вала, хв: | |
Номінальна При максимальному моменті, що крутить на холостому ході, не більше: мінімальна максимальна |
|
модель ТНВД | 337-40 |
модель форсунки | 273-30 |
Тиск початку підйому голки форсунки, МПа (кгс / см): - в експлуатації, не менше - нової (заводського регулювання) |
21,37-22,36(218-228) |
Висока літрова потужність і низький питома витратапалива досягнуті форсуванням двигуна по частоті обертання, застосуванням досконалого сумішоутворення, високого ступеня стиснення і використанням тороидальной камери згоряння.
Трудомісткість технічного обслуговування двигуна в процесі експлуатації значно знижена завдяки застосуванню закритої системиохолодження з всесезонной спеціальної охолоджувальною рідиною, високоякісних моторних масел двоступеневого фільтра повітря сухого типу, ефективних паливних і масляних фільтрів.
Високі пускові якості двигуна при низьких температурахзабезпечені застосуванням акумуляторних батарейпідвищеної ємності, потужного стартера, малов'язкого моторного масла і системи передпускового розігріву двигуна.
Двигун складається з кривошипно-шатунного механізму і механізму газорозподілу і систем змащення, охолодження, розігрівання, харчування паливом, харчування повітрям і випуску відпрацьованих газів.
2. Пристрій кривошипно-шатунного механізму
Колінчастий вал (рис.1) виготовлений з високоякісної сталі і має п'ять корінних і чотири шатунні шийки, загартованих ТВЧ, які пов'язані між собою щоками і сполучаються з ними перехідними галтелями. Для рівномірного чергування робочих ходів розташування шатунних шийок колінчастого вала виконано під кутом 90 °.
До кожної шатунной шийці приєднуються два шатуна: один для правого і один для лівого рядів циліндрів (рис.2).
Підведення масла до шатунних шийок проводиться від отворів в корінних шийках 10 прямими отворами 11.
Для врівноваження сил інерції і зменшення вібрацій колінчастий вал має шість противаг, відштампованих заодно зі щоками колінчастого вала. Крім основних противаг, є два додаткових знімних противаги 1 і 2. напресованих на вал, при цьому їх кутове розташування щодо колінчастого вала визначається шпонками 5 і 6 (рис.1).
У розточення хвостовика колінчастого вала запресований кульковий підшипник 5 (рис.2).
Рис.1. Колінчастий вал.

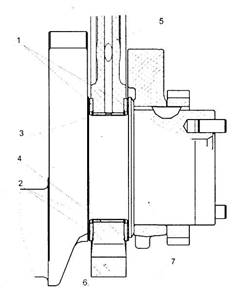
Рис.2. Установка наполегливих півкілець і вкладишів підшипників колінчастого вала.
У порожнину переднього носка колінчастого вала ввернуть жиклер 8. через калібровонное отвір якого здійснюється мастило шліцьового валика відбору потужності на привід гідромуфти.
Від осьових переміщень колінчастий вал зафіксований двома верхніми півкільцями 1 і двома нижніми півкільцями 2 (рис.2), встановленими в проточках задньої корінний опори блоку циліндрів, так що сторона з канавками прилягає до наполегливою торцях валу. На передньому і задньому шкарпетках колінчастого вала (рис.1) встановлено шестерня 3 приводу масляного насоса і ведуча шестерня 4 приводу розподільного вата. Задній торець колінчастого вала має вісім різьбових отворів для болтів кріплення маховика, передній носок колінчастого валу має вісім отворів для кріплення гасителя крутильних коливань.
Ущільнення колінчастого вала здійснюється гумовою манжетою 8 (рис.3), з додатковим ущільнюючим елементом - пилюжником 9. Манжета розміщена в картері маховика 4. Манжета виготовлена з фторкаучука за технологією формування робочої ущільнюючої кромки безпосередньо в прессформе.
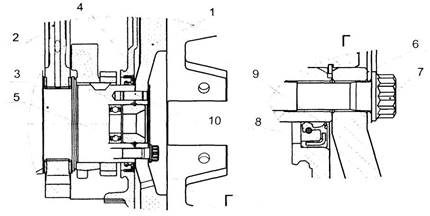
Рис.3. Установка маховика і манжети ущільнення колінчастого вала.
Діаметри шийок колінчастого вала: корінних 95 ± 0.011 мм. шатунних 80 ± 0,0095 мм. Для відновлення двигуна передбачені вісім ремонтних розмірів вкладишів.
Вкладиші 7405.1005170 Р0.7405.1005171 Р0.7405.1005058 РВ застосовуються при відновленні двигуна без шліфування колінчастого вала. При необхідності шийки колінчастого вала заполіровивается. Допуски на діаметри шийок колінчастого вала, отворів в блоці циліндрів і отворів в нижній головці шатуна при проведенні ремонту двигуна повинні бути такими ж, як у номінальних розмірів нових двигунів. Корінні і шатунні підшипники виготовлені зі сталевої стрічки покритої шаром свинцювата бронзи товщиною 0.3 мм, шаром свінцовооловяністого сплаву товщиною 0.022 мм і шаром олова завтовшки 0.003 мм. Верхні 3 (рис.2) і нижні 4 вкладиші корінних підшипників не взаємозамінні. У верхньому вкладиші є отвір для підведення масла і канавка для його розподілу. Обидва вкладиша 4 нижньої головки шатуна взаємозамінні. Від провертання і бічного зсуву вкладиші фіксуються виступами (вусами), що входять в пази, передбачені в ліжках блоку, кришках підшипників і в ліжках шатуна. Вкладиші мають конструктивні відмінності, спрямовані на підвищення їх працездатності при форсуванні двигуна турбонаддувом, при цьому змінена маркування вкладишів на 7405.1004058 (шатунні), 7405.1005170 і 7405.1005171 (корінні). Тому при проведенні ремонтного обслуговування не рекомендується заміна вкладишів на серійні з маркуванням 740.100. ., Так як при цьому відбудеться суттєве скорочення ресурсу двигуна.
Кришки корінних підшипників (рис.4) виготовлені з високоміцного чавуну марки ВЧ50. Кріплення кришок здійснюється за допомогою вертикальних і горизонтальних стяжних болтів 3, 4, 5, які затягуються за певною схемою регламентованим моментом.
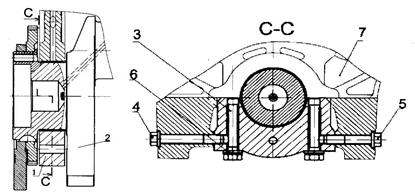
Рис.4 Установка кришок підшипників колінчастого вала.
Шатун (рис.5) сталевий, кований, стрижень 1 має двотавровий розтин. Верхня головка шатуна нероз'ємна, нижня виконана з прямим і плоским роз'ємом. Шатун остаточно обробляють в зборі з кришкою 2. тому кришки шатунів невзаємозамінні. У верхню головку шатуна запресована сталебронзовая втулка 3, а в нижню встановлені змінні вкладиші 4. Кришка нижньої головки шатуна кріпиться за допомогою гайок 6, навернених на болти X попередньо запресовані в стрижень шатуна. Затягування шатунних болтів здійснюється за схемою, визначеною в додатку 8. На кришці і стрижні шатуна нанесені мітки спаренности - тризначні порядкові номери. Крім того на кришці шатуна вибитий порядковий номер циліндра.
Маховик 1 (Рис.6) закріплений вісьмома болтами 7 шатуна, (рис.7), виготовленими з легованої сталі з дванадцятигранний головкою, на задньому торці колінчастого вала і точно зафіксований двома штифтами 10 і настановної втулкою 3 (Рис.6).
З метою виключення пошкодження поверхні маховика під головки болтів встановлюється шайба 6 (рис.7). На оброблену циліндричну поверхню маховика напрессован зубчастий вінець 2, з яким входить в зачеплення шестерня стартера під час пуску двигуна (Рис.6).
При виконанні регулювальних робіт по установці кута випередження впорскування палива і величин теплових зазорів в клапанах маховик фіксується за допомогою фіксатора (рис.7).
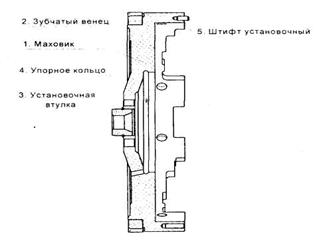
Рис.6. Маховик.
При цьому конструкція має наступні основні відмінності від серійної:
Змінено кут розташування паза під фіксатор на зовнішній поверхні маховика;
Збільшено діаметр розточення для розміщення шайби під болти кріплення маховика.
Розглянуті двигуни можуть комплектуватися різними типами зчеплень. На рис. Маховик показаний для диафрагменного зчеплення.

Рис.7 Положення ручки фіксатора маховика.
а) при експлуатації;
б) при регулювання, в зачепленні з маховиком
Гаситель крутильних коливань закріплений вісьмома болтами 2 (рис.8) на передньому шкарпетці колінчастого вала. З метою виключення пошкодження поверхносгі корпусу гасителя під болти встановлюється шайба 5. Гаситель складається з корпусу (див. Малюнок) в який встановлений з зазором маховик. Зовні корпус гасителя закритий кришкою. Герметичність забезпечується закачуванням (зварюванням) по стику корпусу гасителя і кришки. Між корпусом гасителя і маховиком знаходиться високовязкостная силіконова рідина, дозовано заправлена перед заваркою кришки. Центрування гасителя здійснюється шайбою, привареною до корпусу (рис.9). Гасіння крутильних коливань колінчастого вала відбувається шляхом гальмування корпусу гасителя, закріпленого на шкарпетці колінчастого вала, щодо маховика в середовищі силіконової рідини. При цьому енергія гальмування виділяється у вигляді теплоти. При проведенні ремонтних робіткатегорично забороняється деформувати корпус і кришку гасителя. Гаситель з деформованим корпусом або кришкою до подальшої експлуатації не придатний.
Поршень 1 (рис.10) відлитий з алюмінієвого сплаву зі вставкою із зносостійкого чавуну під верхнє компресійне кільце.
У голівці поршня виконана тороїдальна камера згоряння з витіснювачем в центральній частині, вона зміщена щодо осі поршня в сторону від виточок під клапани на 5 мм.
Бічна поверхня являє собою складну овально-бочкообразную форму із заниженням в зоні отворів під поршневий палець. На спідницю нанесено графітове покриття.
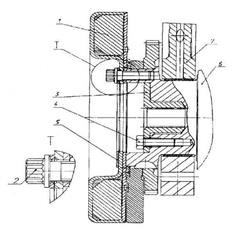
Рис.8 Установка гасителя крутильних коливань колінчастого вала.
1 - гаситель; 2 - болт кріплення гасителя; 3 - полумуфта відбору потужності;
4 - болт кріплення напівмуфти; 5 - шайба; 6 - колінчастий вал; 7 - блок циліндрів.
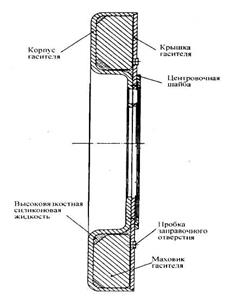
Рис.9 Гаситель крутильних коливань колінчастого вала.

Рис.10 Поршень з шатуном і кільцями в зборі.
1 - поршень; 2 - маслос'емноє кільце; 3 - поршневий палець; 4, 5 - компресійні кільця; 6 - стопорне кільце.
У нижній її частині виконаний паз, що виключає при правильній збірці контакт поршня з форсункою охолодження при знаходженні в НМТ.
Поршень комплектується трьома кільцями, двома компресійними і одним маслос'емниє. Відмінною його рисою є зменшена відстань від днища до нижнього торця верхньої канавки, яке становить 17 мм. На двигунах, з метою забезпечення паливної економічності та екологічних показників, застосований селективний підбір поршнів для кожного циліндра по відстані від осі поршневого пальця до днища. За вказаною параметру поршні розбиті на чотири групи 10, 20, 30 і 40. Кожна наступна група від попередньої відрізняється на 0,11 мм. У запасні частини поставляються поршні найбільшої висоти, тому щоб уникнути можливого контакту між ними і головками циліндрів в разі заміни необхідно контролювати надпоршневій зазор. Якщо зазор між поршнем і головкою циліндра після затяжки болтів її кріплення буде менш 0,87 мм необхідно підрізати днище поршня на відсутню до цього значення величину. Поршні двигунів 740.10, 740.11 і 740.13 відрізняються один від одного формою канавок під верхнє компресійне і маслос'емноє кільця, (див. Розділи компрессионное і маслос'емноє кільця). Установка поршнів з двигунів КАМАЗ 740.10 і 7403.10 неприпустима. Допускається установка поршнів з поршневими кільцями двигунів 740.11 і 740.13 на двигун 740.10.
Компресійні кільця (рис.10) виготовляються з високоміцного, а маслос'емноє з сірого чавунів. На двигуні 740.10 форма поперечного перерізу компресійних кілець одностороння трапеція, при монтажі похилий торець з відміткою "верх" повинен розташовуватися з боку днища поршня. На двигунах 740.10 і 740.13 верхнє компресійне кільце має форму перетину двосторонньої трапеції з вибіркою на верхньому торці, який повинен розташовуватися з боку днища поршня.
Робоча поверхня верхнього компресійного кільця 4 покрита молібденом і має бочкоподібні форму. на робочу поверхнюдругого компресійного 5 і маслос'емного кілець 2 завдано хром. Її форма на другому кільці є конус з ухилом до нижнього торця, з цього характерній ознаці кільце отримало назву "хвилинне". Хвилинні кільця застосовані для зниження витрати масла на чад, їх установка в верхню канавку не припустима.
Маслос'емноє кільце коробчатого типу з пружинним розширювачем, які мають змінний крок витків і шліфовану зовнішню поверхню. Середня частина розширювача з меншим кроком витків при установці на поршень повинна розташовуватися в замку кільця. На двигуні моделі 740.11 висота кільця - 5 мм а на двигунах 740.10 і 740.13 висота кільця - 4 мм.
установка поршневих кілецьз інших моделей двигунів КАМАЗ може привести до збільшення витрати масла на чад.
Для виключення можливості вживання не взаємозамінних деталей циліндропоршневої групи при проведенні ремонтних робіт рекомендується використовувати ремонтні комплекти:
7405.1000128-42 - для двигуна 740.10 - 240;
740.13.1000128 і 740.30-1000128 - для двигунів 740.11-260 і 740.13-300.
В ремонтний комплект входять:
поршень;
Поршневі кільця;
Поршневий палець;
Стопорні кільця поршневого пальця
Гільза циліндра;
Ущільнювальні кільця гільзи циліндра.
Форсунки охолодження встановлюються в картерной частини блоку циліндрів і забезпечують подачу масла з головної СГ) масляної магістралі при досягненні в ній тиску 0,8 - 1,2 кг / см2 (на такий тиск відрегульований клапан, розташований в кожної з форсунок) у внутрішню порожнину поршнів .
При складанні двигуна необхідно контролювати правильність положення трубки форсунки щодо гільзи циліндра і поршня. Контакт з поршнем неприпустимий.
Поршень з шатуном (рис.10) з'єднані пальцем 3 плаваючого типу, його осьовий переміщення обмежене стопорними кільцями 6. Палець виготовлений із хромонікелевої сталі, діаметр отвору 22 мм. Застосування пальців з отвором 25 мм неприпустимо, оскільки це порушує балансування двигуна.
3. Розбирання, ремонт та збирання шатунно-поршневої групи
До закінчення гарантійного терміну не розбирайте двигун (не знімайте головки циліндрів, масляний картер, не порушуйте пломби паливного насосависокого тиску і не розбирайте його), в іншому випадку втрачається право на гарантійний ремонтдвигуна. При необхідності допускається замінювати топлівопроводи високого і низького тиску, шланги, фільтри очищення масла, палива і повітря, водяний насос, вентилятор, вимикач гідромуфти, зовнішні кріпильні деталі, впускні повітропроводи і випускні колектори, водозбірні труби, форсунки, штанги штовхачів, турбокомпресори;
Перед установкою двигуна на стенд зніміть масляний фільтр з теплообмінником, вентилятор, випускні колектори, кронштейни передніх опор, стартер. Поверхні, що труться деталей, крім обумовлених особливо, при складанні змащуйте моторним маслом.
Неметалеві прокладки для зручності складання, при необхідності, ставте з нанесенням на одну з деталей, що мастила. Слідкуйте, щоб прокладки рівномірно прилягали до сполучаються поверхонь, були щільно затиснуті і не виступали за контур сполучених поверхонь.
При установці гумові кільця ущільнювачів і заходная фаски деталей, змащуйте змазкою;
Чи не підгинайте шпильки при надяганні на них деталей.
Поршень з кільцями і шатуном в зборі встановлюють в лещата і за допомогою знімача І-801.08.000 знімають з поршня кільце компресійне верхнє, кільце компресійне і кільце маслос'емноє в зборі. При необхідності заміни поршня або шатуна виймають стопорне кільце поршневого пальця з бобишек поршня і виймають поршень з шатуном в зборі з лещат.
Нагрівання поршень протягом 10 хв в масляній ванні до температури 80 ... 100 ° С, випрессовивают за допомогою вибивання поршневий палець. Деталі шатунно-поршневої групи миють і дефектуют.
Поршень бракують при наявності тріщин, прогарів, руйнуванні днища, вкраплення сторонніх часток, а також при зносі:
Спідниці поршня в площині, перпендикулярній осі пальця, на відстані 104 мм від днища - до розміру менше 119,81 мм;
Отвори під поршневий палець - до діаметра більше 45,02 мм;
Канавки верхнього компресійного кільця - до розміру, що вимірюється по вкладеним в канавку роликам діаметром 2,96 мм, менш 120,25 мм;
Канавки нижнього компресійного кільця - до розміру, що вимірюється аналогічно, менш 120,7 мм;
Канавки маслос'емного кільця - до висоти понад 5,1 мм;
Зовнішньої поверхні - до діаметра менше 44,99 мм.
Поршневий палець бракують при наявності відколів, тріщин, рисок, забоїн і слідів корозії на поверхні і торцях, а також при зносі зовнішньої поверхні до діаметра менше 44,99 мм, В останньому випадку деталь слід направити на відновлення.
Шатун в зборі бракують при наявності тріщин або обломів, знос торців нижньої головки по ширині до розміру менше 33,23 мм. Вигин і скручування шатуна визначають за допомогою пристосування 30701. При непараллельности осей отворів головок шатуна на довжині 100 мм більше 0,06 мм шатун бракують або направляють на відновлення.
При зносі отвори у втулці верхньої головки шатуна до діаметра більше 45,04 мм втулку випрессовивают і встановлюють нову бронзову втулкутаким чином, щоб масляні отвори у втулці і шатуне збігалися. Перед установкою втулку охолоджують до температури мінус 50 ° С. Запресовування втулки не допускається. Отвір у встановленій втулки розточують до діаметра 45 + 8; 4 мм при частоті обертання розточний головки 1600 хв і подачі 0,06 мм / оборот. Відновлений шатун промивають і обдувають стисненим повітрям. При зносі отвори у верхній голівці шатуна під втулку до діаметра більше 49,02 мм шатун бракують або направляють на відновлення. При зносі отвори нижньої головки шатуна до діаметра більше 85,02 мм його обробляють до ремонтного розміру 85,5 мм, а при діаметрі більше 85,535 мм - бракують або направляють на відновлення.
Перед складанням шатунно-поршневої групи поршневі пальці підбирають до шатунам. Поршень нагрівають в маслі до температури 80 ... 100 ° С, поміщають в пристосування для збірки і з'єднують з шатуном поршневим пальцем, встановивши шатун так, щоб виточки під клапани в поршні і пази під вуса вкладишів на шатуне були розташовані з одного боку. Запресовування поршневого пальця не допускається. Перед складанням поверхні, що сполучаються поршневого пальця і отворів в поршні змащують тонким шаром чистого моторного масла М ЮГгк.
У канавки поршня встановлюють стопорні кільця поршневого пальця. На поршень за допомогою пристосування для зняття і установки кілець послідовно встановлюють маслос'емноє і компресійні кільця (рис.10). При монтажі маслос'емного кільця в канавку поршня встановлюють розширювач і потім надягають маслос'емноє кільце так, щоб стик розширювача знаходився діаметрально протилежно замку кільця. Компресійні кільця встановлюють на поршень скошеної стороною і клеймом "верх" до днища поршня. Замки сусідніх кілець розташовують під кутом 120 ° С. Перед установкою кілець видаляють нагар з канавок поршня, а після установки перевіряють легкість переміщення кілець в канавках.
Шатун також повинен вільно переміщатися навколо осі поршневого пальця. При дотриманні цих вимог поршень в зборі з шатуном знімають з пристосування і передають на складання двигуна.
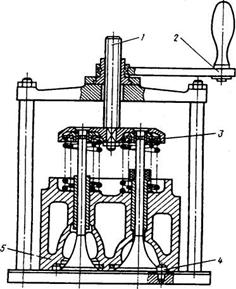
Рис.11. Розбирання головки циліндрів в пристосуванні І-801.06.000
1 - гвинт; 2 - рукоятка; 3 - тарілки клапанів; 4 - штифт; 5 - головка циліндрів.
Головку циліндрів встановлюють на пристосування для розбирання-збирання 7831-4044 або верстак. Разогнув вусики стопорною шайби кріплення стійки коромисел, відкручують гайки кріплення стійок осі коромисел і знімають стійку коромисел, стопорні шайби і фіксатор коромисел, а потім - коромисла клапанів зі стійки коромисел. Відвернувши і знявши гайку 10 регулювального гвинта, вкручують регулювальний гвинт 8 коромисла, знімають головку циліндрів з пристосування для розбирання-збирання і встановлюють на пристосування для зняття-встановлення клапанів (рис.11) так, щоб штифти 4 увійшли в отвори під болти кріплення головки.
Обертанням рукоятки пристосування віджимають тарілки пружин клапанів разом з втулками і знімають сухарі клапанів, тарілки з втулками, зовнішні і внутрішні пружини і шайби пружин клапанів. З направляючої втулки впускного клапана знімають ущільнювальну манжету в зборі, після чого з головки циліндрів витягують впускні і випускні клапани.
При необхідності заміни вивертають наступні деталі: ввертиш кріплення впускного колектора, Ввертиш кріплення водяної труби, шпильки кріплення патрубка випускного колектора, шпильки кріплення стійок коромисел і шпильки кріплення скоби форсунки. Головку циліндрів знімають з пристосування.
Головку циліндрів і зняті деталі миють, клапани, сідла і направляючі втулки клапанів очищають від нагару, обдувають деталі стисненим повітрям і дефектуют.
Головку циліндрів встановлюють на стенд для опресовування 470.085 і перевіряють під тиском повітря 0,3 МПа (3 кгс / см) протягом 2 хв герметичність сорочки охолодження і під тиском 0,6 ... 0,65 МПа (6 ... 6, 5 кгс / см) - герметичність масляних каналів. При витоку повітря головку циліндрів бракують. Вона також підлягає вибракуванню при наявності тріщин, захоплюючих внутрішні канали, порожнини отворів під форсунку, направляючі втулки і поверхню сполучення з блоком циліндрів, при руйнуванні посадочних місць під сідла клапанів і перемичок між ними, при пошкодженні або гравітаційному руйнуванні поверхні сполучення з блоком циліндрів.
При наявності вироблення або раковин на робочій поверхні сідел клапанів їх обробляють до виведення дефекту притиранням, не допускаючи збільшення діаметра сідла випускного клапана більше 43 мм, а впускного - 48 мм. При неможливості усунення дефекту сідла замінюють.
При наявності тріщин, сколів, механічних пошкоджень на поверхні напрямних втулок клапанів, а також при зносі отвори в направляючої втулці до діаметра більше 10,04 мм втулку заміняють. Також підлягає заміні при прогорании або механічному пошкодженні кільце ущільнювача газового стику.
Кришку головки циліндрів бракують при наявності обломів і тріщин. Неплощинність поверхні прилягання до голівці циліндрів перевіряють щупом на повірочної плиті. Вона повинна становити не більше 0,15 мм. В іншому випадку поверхня обробляють до усунення дефекту, знімаючи шар металу не більше 0,5 мм. При неможливості усунення дефекту деталь бракують.
Коромисло клапана з втулкою в зборі бракують при наявності обломів або тріщин, а також при зносі носка коромисла по висоті. Відстань від горизонталі, що проходить через центр отвору у втулці коромисла, до носка коромисла, має бути не більше 6,0 мм. При зносі отвори у втулці її замінюють і обробляють під ремонтний розмір відповідно до ремонтним розміром стійки коромисел.
Стійку коромисел бракують при наявності обломів або тріщин. При зносі опорних поверхонь їх обробляють до ремонтного розміру, при діаметрі більше 24,66 мм - бракують.
Клапани впускний і випускний бракують при наявності тріщин, обломів, знос або вигорянні робочої фаски клапана. При зносі стрижня впускного клапана до діаметра менше 9,94 мм, а випускного - 9,90 мм клапан бракують або направляють на відновлення. При нерівномірному зносі торця стержня клапана його обробляють до усунення дефекту, не допускаючи
зменшення висоти від торця до кільцевої проточки понад 6,3 мм. При неможливості усунення дефекту клапан бракують.
Після усунення дефектів головку циліндрів в зборі з направляючими втулками клапанів поміщають на пристосування для розбирання-збирання 7831-4044 або верстак і встановлюють на місце, якщо вони були зняті, такі деталі: шпильки кріплення патрубка випускного колектора (висота виступанія шпильок 52 ± 1 мм) , шпильки кріплення скоб форсунки, шпильки кріплення стійок коромисел, ввертиш кріплення впускного колектора і ввертиш кріплення водяної труби. Головку циліндрів знімають з пристосування для збірки і встановлюють на стенд для притирання клапанів сідлами клапанів вгору.
Приготувавши притирочную пасту з 81% електрокорунду зернистого і 13% парафіну, розведених в моторному маслі МЮГгк до сметанообразного стану, наносять пасту на робочу поверхню сідел клапанів. Встановивши впускний і випускний клапани в головку циліндрів, виконують їх притирання до тих пір, поки на фасках клапана і сідла чи не з'явиться безперервний матовий поясок шириною не менше 1,5 мм без рисок і розривів на поверхні паска. При правильній притирке матовий поясок на сідлі повинен починатися біля основи великого конуса сідла.
Головку циліндрів і клапани укладають в тару, осередки якої пронумеровані і забезпечують збереження приналежності клапанів і сідел, до яких вони прітерти. Деталі промивають в миючому розчині КМ-1 з піногасником ЕАП-40. Концентрація КМ-1 - 5 г / л, ЕАП-40 - 0.2 ... 0.3%. Склад миючого розчину: карбонат натрію - 22,5%, тринатрийфосфат - 18,9%, триполіфосфат натрію - 50,6%, сульфонал - 2,3%, Синтанол ДТ-7 - 5,7%. Температура миючого розчину 70 ... 80 ° С, час витримки 2 хв.
Після мийки головку циліндрів встановлюють на пристосування для зняття-встановлення клапанів (див. Рис.11), змащують стрижні клапанів і робочі поверхні направляючих втулок чистим моторним маслом і встановлюють клапани на свої місця згідно з нумерацією після притирання.
На направляючу втулку впускного клапана встановлюють ущільнювальну манжету в зборі, встановлюють шайби пружин клапанів, внутрішні і зовнішні пружини, тарілки пружин клапанів з втулками і обертанням рукоятки пристосування стискають пружини з тарілками і втулками. Встановивши сухарі клапанів, відпускають пружини стежачи за тим, щоб сухарі увійшли у втулку.
Знявши головку циліндрів з пристосування, перевіряють герметичність клапанів. Для цього головку циліндрів встановлюють по черзі впускними і випускними вікнами вгору і заливають в них дизельне паливо. Добре притерті клапани не повинні пропускати паливо в місцях ущільнення протягом 30 с. При подтекании палива слід постукати гумовим молотком по торця клапана. Якщо підтікання не зникає, клапани необхідно притертися повторно. Якість притирання можна перевірити на олівець, для чого поперек фаски клапана на рівній відстані наносять шість-вісім рисок. Клапан вставляють в сідло і, сильно натиснувши на нього, повертають на 1/4 обороту. При гарній притирання все риски повинні бути стерті.
ВИСНОВОК
Кривошипно-шатунний механізм є основним механізмом поршневого двигуна. Він служить для сприйняття тиску газів в такті робочого ходу і перетворення зворотно-поступального руху поршнів в обертальний рух колінчастого вала. Він складається з блок-картера, гільз і головок циліндрів, поршнів з кільцями і поршневими пальцями, шатунів, колінчастого вала, корінних і шатунних підшипників і маховика.
Маховик виготовлений зі спеціального сірого чавуну. Зубчастий вінець напрессован на маховик з попереднім нагріванням. Маховик закріплений на задньому торці колінчастого вала болтами і зафіксований двома штифтами і настановної втулкою.
Шатуни - сталеві, двотаврового перетину. З'єднання нижньої головки шатуна з кришкою виконано з прямим плоским роз'ємом.
Поршні відлиті з висококремниста алюмінієвого сплаву і оснащені чавунною зміцнюючої вставкою під верхнє компресійне кільце і колоїдно-графітним пріработочним покриттям спідниці. На поршні встановлені два компресійних і одне маслос'емних кільця. Компресійні кільця виготовлені з чавуну спеціального хімічного складу, перетин кільця являє собою односторонню трапецію. Бічна робоча поверхня верхнього компресійного кільця покрита хромом, нижнього - молібденом. Маслос'емноє кільце має прямокутний перетин, кручений пружинний розширювач і хромовану робочу поверхню. При складанні двигуна забезпечується виступаніє поршня над ущільнювача торцем гільзи циліндра.
Поршневі пальці виготовлені з хромонікелевої сталі у вигляді пустотілих циліндричних стрижнів і зміцнені цементацией і загартуванням. Осьове переміщення пальця в поршні обмежено стопорними кільцями.
Список використаних джерел
1. Аймасов Н.У., Гатауллін Н.І. Двигуни автомобілів КамАЗ. - Набережні Човни, 2002 г.
2. Барун В.Н., Азаматов Р.А. Технічне обслуговування та ремонт Автомобілів КамАЗ. - 2-е вид. перераб і додат. - М .: Транспорт, 1987.
3. Карагодин В.І., Карагодин Д.В. Автомобілі КамАЗ: пристрій, технічне обслуговування та ремонт. - М .: Транспорт, 2001. - 342 с.
4. Медведков В.І., Білик С.Т. Автомобілі КамАЗ - 5320: Навчальний посібник. - М .: Видавництво ДОСААФ, 1999..
5. Керівництво по експлуатації та технічного обслуговування двигунів КамАЗ серії В: Бюлетень, 1996..